WH Gittins & Son, based in Ruyton-XI-Town, Shropshire, operates across more than 1,500ha of owned, contract-farmed and farm business tenancy land, growing a mix of cereals and forage crops, as well as energy crops for the farm’s 1.9MW anaerobic digester.
A key crop for the business is lucerne, according to renewables manager Sam Dutton, which is cut, picked up with a forage wagon and moved to drying floors, before being baled and sold to high-yielding dairy farms.
“Lucerne is a delicate crop, so we couldn’t risk cutting and raking because that would lead to leaf losses,” Sam explains.
Initially, the farm brought in a contractor with mowers and groupers.
This showed that the system would work well in lucerne, but timing the operation around weather windows and the contractor’s availability proved to be tricky. The farm decided to look at bringing the operation in-house.
“With lucerne, we need to be flexible,” Sam says. “We base the area cut on the predicted yield and the capacity of the drying floors, meaning sometimes we go back out and drop another couple of hectares at short notice. This wasn’t always possible when using a contractor.”
Versatility in use
They sourced a demonstration Kverneland 53100MT from local dealer Battlefield Machinery and were quickly impressed with the versatility of the machine.
“There was a little bit of concern about the conditioner and whether this would damage the lucerne,” says Sam. “However, with the conditioner set all the way back, it acts as an accelerator for the crop, pushing it onto the grouper belts.”
This was an important factor, as the mowers would be used across multiple crops, including grass for silaging and forage and hybrid rye, meaning the triple mowers required a conditioning unit.
As the farm can keep this on the mower when working in lucerne, it saves significant downtime between crops and allows the farm to move quickly when weather windows allow.
Similarly, when working in crops that need to be spread out for drying, the groupers can be lifted out of work via the Isobus terminal, maintaining that flexibility.
“The drying floors can hold 200-240t of lucerne, and we mow at 20-24% moisture to retain the correct levels of protein,” Sam says.
“With the Kverneland mower/groupers we can quickly drop another area of the field to keep the drying floors at capacity, even if we’re working in other crops at the time.”
He adds that the mowers do require an experienced operator on the seat. “Because you’re dropping the swath and not touching it again, there is no opportunity to fix tight corners, and when you’re working around the obstacles, the operator must know how to adjust the working width of the mowers to ensure no grass is missed.
“However, this isn’t unique to Kverneland and appears to have been fixed with the Curve Pilot offered on newer machines.”
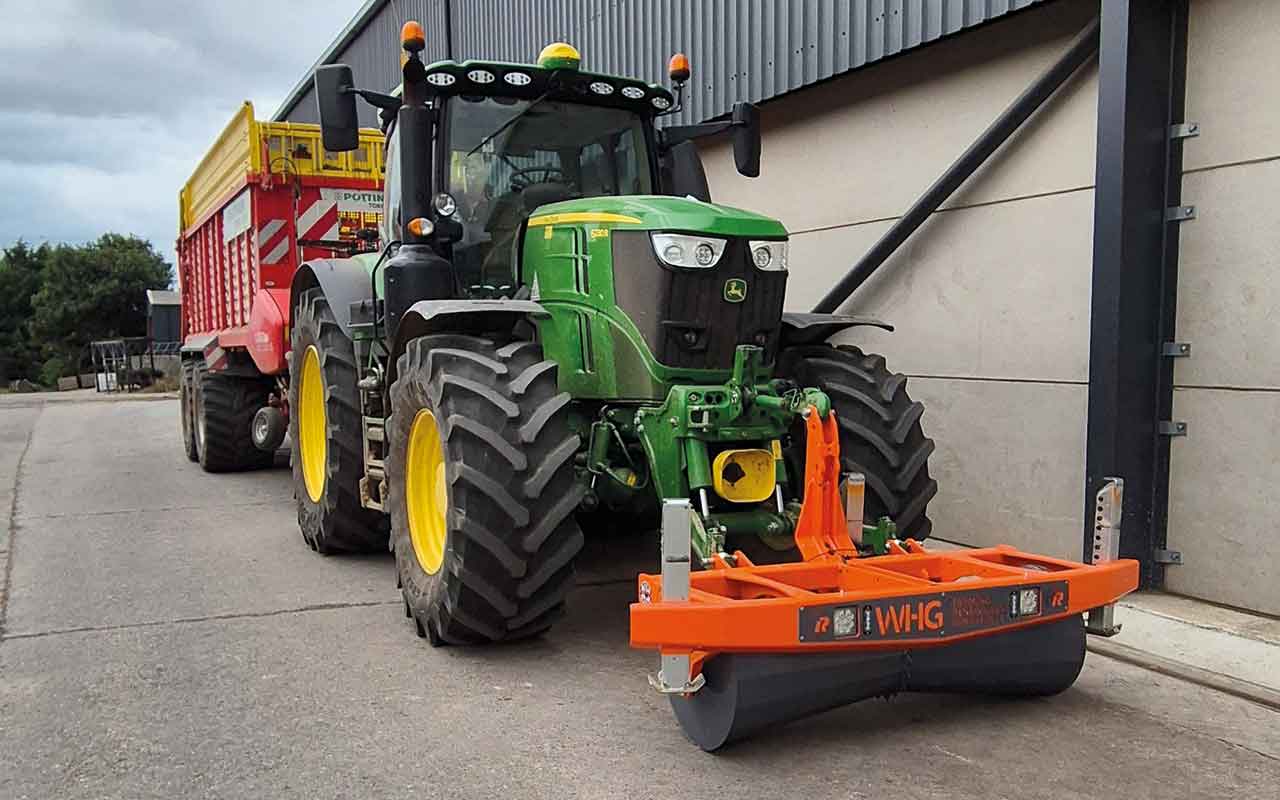
In-house operation
Mowing wasn’t the only part of the operation brought in-house. As well as the Kverneland triple mowers, the company invested in a Pottinger forage wagon, which lifts the crop without the chopping unit engaged and brings it back to the drying floors.
Lucerne is then dried down to about 10% moisture content, being turned once a day, before a contractor is brought in to bale the crop in the yard.
Forage rye crops are occasionally mown using the groupers, although this depends on the prevailing conditions, and when more drying is needed, the groupers are lifted and the farm reverts to a standard rotary rake.
The use of forage and energy crops on farm have been key to helping the business become more self-sufficient in terms of energy use, with dairy waste and manures imported from local farms in exchange for crops to feed the digesters, along with excess lucerne and ryegrass.
The main rotation comprises winter wheat, maize, rye and, for the first time this season, beans.
Breaks of sugar beet are used for additional digester feed, with stubble turnips and westerwolds used as cover and rented out for grazing.