Since 2021, Bourgault Tillage Tools (BTT) UK has been providing after-market wearing parts, using a product range developed and tested by its Canadian parent company.
The company has not only found success offering hard-wearing components to farming and contracting businesses, but is also working with UK manufacturers such as Fentech and Grange Machinery to provide wearing metal for new products coming to market.
Heading out to a farm near Oundle, we met up with farm owner Charles Simpson and operator Simon Mould, of DJL Simpson, who are operating a 6.4m mounted Weaving Sabre tine drill and an 8m Weaving toolbar with front tank.
“We like the Weaving design,” explains Charles. “They’re solidly built and have enabled us to get crops in the ground over the past two seasons when many people in the area have struggled.”
While the machine impressed them, the hard, abrasive soils caused wearing issues.
“The legs would wear, and it would start to eat away at the seed tubes,” Simon says. “We were having to change each tube two to three times for every leg.”
They noted that the company stood by the machines and helped with teething troubles, but they could see the wearing parts were quickly going to eat into the margins.
As BTT UK was based nearby, they approached managing director Ian Clayton-Bailey for a solution.
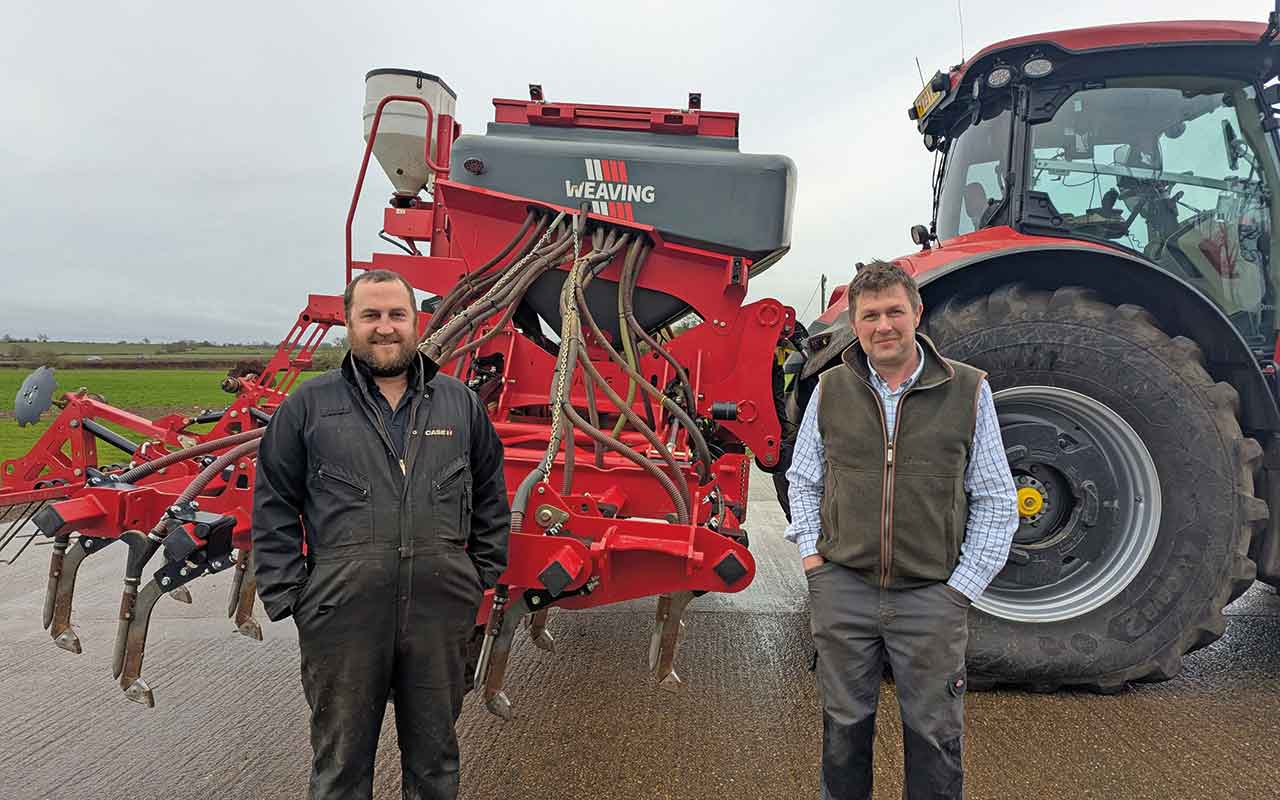
Protecting parts
For this season, the 6.4m Weaving has been fitted with BTT points and legs, splitting the wearing metal into two parts, rather then the single-piece coulter fitted as standard.
Both BTT parts have extra protection, with either tungsten carbide or strategically placed hardened weld strips. “The point engages with the soil, which protects the leg and, in turn, protects the seed pipe,” Ian says.
So far, the BTT points have completed just over 600ha, including 160ha of beans sown at a 6in depth. “Previously, we would have been replacing a leg a year,” Simon says.
“But I don’t think the points are half worn yet, and the leg is almost entirely intact. There is a little bit of wear around the seed tubes because of the depth we work at for the beans, but we haven’t changed one yet.”
With the point in place to crack the soil before the leg passes through, Simon says the drill is also easier to pull.
While it is difficult to quantify, he believes they have been using less fuel, and this has influenced the decision to lower the horsepower up front. Instead of a John Deere 8400R, a new Case Puma 240 CVX will be used, once again cutting costs.
“The point is doing 70% of the work and moving the soil around the legs, creating a boiling effect that leaves more tilth and better germination without disturbing the soil between the rows,” Simon adds.
“We trialled it on the 8m toolbar as well, just three legs on the one side, and you could see the difference in the field.”
Saving time and money
The key benefits for Charles have been the reduction in maintenance costs. He says the BTT parts cost almost the same as the Weaving originals, so the savings made by not having to replace them regularly directly affects the bottom line.
Not having multiple seed tube changes throughout the season also helps to reduce costs. Ian adds that when new parts do need to be fitted, they should also see a difference in the time it takes.
“The replaceable tips are held in position on the leg with a nut-and-bolt system, so it should only take a few minutes per leg to make the change.”
More importantly, Simon points out they can go out into the field confident they will get consistent performance.
“The windows are so tight now, so any unexpected maintenance can make the difference between getting a good crop in or mauling something in.”
With the 6.4m machine fully kitted out with BTT UK parts, Charles and Simon are waiting for the wearing metal on the 8m toolbar to be up for replacement, at which point they will swap over to BTT parts.