Automation has had an enormous effect in some industries, but its progress on farms is much more limited in spite of more than 60 years of research and development.
Success stories for automation include large-scale manufacturing industries where production lines often have many more robots than people, but the situation remains very different in farming.
One of the few agricultural sectors where robots are well established is in packhouses linked to large-scale vegetable and fruit production, automation also sometimes makes a contribution on dairy farms where robots have taken over in the milking parlour.
See also: Whatever happened to… the Ferguson Black Tractor?
The big challenge for farming with robots is to develop a tractor that can power a range of field equipment without a driver at the controls.
Interest in the idea has increased during the last 20 years or so, with many manufacturers demonstrating experimental driverless tractors, which achieved plenty of publicity but very few sales.
1950s research
In fact, attempts to develop a robotic tractor started back in the 1950s and it was a UK research team that produced the technology resulting in a small number of sales during the 1960s.
The team of agricultural engineers that developed what was almost certainly the world’s first driverless tractor was based at Reading University in Berkshire, and the tractor they modified to operate without a driver was a standard International Harvester B-250 model borrowed from the tractor fleet on one of the University farms.
The project started at some time during the mid-1950s and the result was ready for its first driverless demonstration in about 1957.
Guide wire
Advanced guidance systems such as GPS were not available when the Reading tractor project was at the development stage, and instead the research team relied on a guide wire system to control the tractor.
This used a network of wires buried beneath the soil surface, below cultivation depth, carrying a small electric current that could be detected by a pair of sensors attached to the front of the tractor.
The two sensors controlled the tractor’s steering, following the exact location of the guide wire, while special signals programmed into the wire at appropriate locations carried extra instructions such as when to raise or lower the three-point linkage or to turn the PTO on or off during a headland turn.
There were also a number of safety features built into the guidance system, and these included an emergency control that would stop the tractor if it lost contact with signals from the network of buried wires.
Another safety device was a contact bar mounted at the front of the tractor that would stop the engine immediately if the bar came into contact with a solid object.
This was intended to avoid a mishap with a slumbering cow, for example, but on at least one occasion the demonstration programme included a rather brave lady who stood in front of the slowly approaching tractor to show how effectively the stop control worked.
Demonstrations featuring the driverless tractor were held on the university’s farms, often with an audience that included students from the agricultural courses, and their response to this potential future for farm mechanisation was often extremely sceptical.
National Institute of Agricultural Engineering
Having demonstrated the world’s first driverless tractor, which was the starting point for what is potentially one of the most important developments in tractor history, the university handed the project over to the National Institute of Agricultural Engineering (NIAE) at Silsoe, Bedfordshire.
This was presumably because the NIAE was more likely to have the resources to continue and expand the research and development programme.
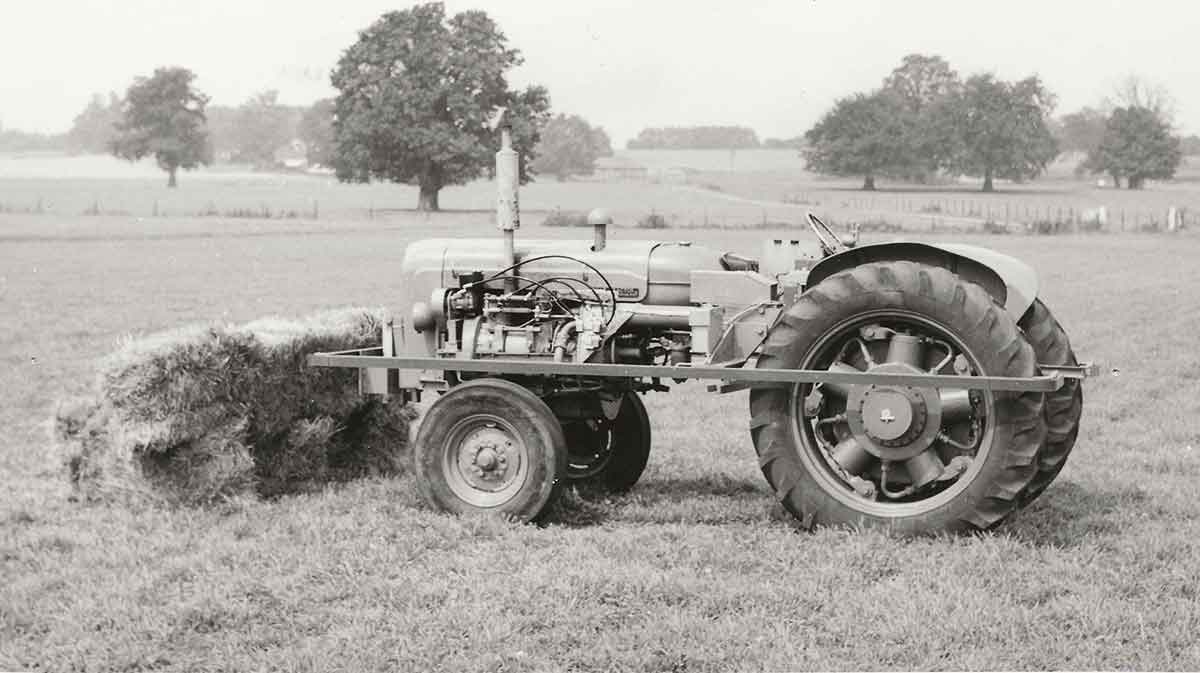
Silsoe engineers adapted the Reading University guidance system to work on a Fordson Major Diesel tractor.
The tractor had previously been modified by the NIAE for a hydrostatic transmission project with a drive system based on wheel motors, and this affected its appearance but was not part of the automatic control function.
Auto-Track
While the NIAE project was progressing during the early 1960s, the possibilities offered by the buried wire guidance system were starting to attract commercial interest, and a new company called Auto-Track was formed to convert standard farm tractors for working with wire guidance developed from the Reading University system.
Auto-Track, which was based in Hampshire, demonstrated its new driverless tractor equipment at the 1969 Royal Show mounted on an MF165 tractor which was on loan from Massey Ferguson.
Obviously, a buried wire guidance system has some limitations for general field work, but it is suitable for grass mowing and this was the task that attracted some customers to the Auto-Track conversion.
Its first customer, who was probably the first person anywhere to buy a driverless tractor, was a fruit grower in Essex who bought the equipment on a Massey Ferguson 135 vineyard tractor for mowing between the trees in his orchards.
For the production version of its tractor control system, Auto-Track used guide wires buried at 20in below the soil surface and carrying an electric current from a standard 12V battery.
The modest sales total for the company’s tractor conversions was about four or five, according to one estimate, with most or perhaps all of them used for grass mowing.
The Auto-Track conversions were the end of the road for tractors using the buried wire guidance system, although basically similar systems are used for routine movement of robot vehicles in industrial premises.
Following the limited success of the Reading University project, enthusiasm for driverless tractor development faded for a while, but the arrival of GPS and other more versatile and advanced guidance technology has brought a resurgence of interest during the past 20 years or so.