Conventional bales are still a key income stream for many farmers and contractors, but the process can be labour-intensive and time-consuming. For those producing tens of thousands of bales a year, a bale accumulator is often the only viable way to protect the quality of hay and straw while working around the weather.
Arcusin
Based just outside Kidlington, Andrew Haynes has used an Arcusin Multipack bale accumulator for more than 15 years. Having previously used flat-eights and manual stacking, the decision was made after a brutally hot summer to look at improving the efficiency of conventional baling.
Hay and straw bales make up a significant proportion of the workload, with about 400ha of grassland made into hay, and another 600ha of cereal ground made into straw, sold into local stable yards and hauled across the country. Andrew initially started with a Multipack B14 accumulator, having looked at the other machines on the market.
“The Arcusin seemed to be the most flexible, as it could handle some variation in the length of the bales,” he explains. “At the time, it was also the only machine that you didn’t have to tow directly behind the baler, which was significant as we try to run two balers.”
He adds that the B14 could be a little rough with the bales, but the benefits far outweighed this, enabling the business to bale more when the weather was right, safe in the knowledge that everything would be under cover by the end of the day.
The B14 stayed on farm for 10 years. On the lookout for another machine, Andrew agreed to hold a demonstration of the Multipack C14+ model on the farm.
“We were so impressed with it that the demo machine never left.”
Less than six years after purchasing the C14+, Andrew says he was convinced to look at the latest Multipack E14 accumulator. “I didn’t think you could improve what we had,” he explains.
“We were packing 25,000 bales a year and, when conditions allowed, we could pack 3,000 a day, but when I looked at the E14, it was clear that Arcusin had made some serious updates.”
He says the previous machine would occasionally struggle with seed hay, because the bales had less grip than coarser varieties.
Another clear benefit was the increased pressure on the bale retaining platform.
“When you put 12 bales into the previous machine, the retainer would occasionally allow bales to drop an inch, which would affect the feeding of the final two bales. I could see straight away that this had been fixed.”
Feed-in boost
The feed-in had also been improved, with sensors to adjust the chain feed and avoid too many bales entering the chamber at once. “All of this means we can pack half as many bales again each day,” Andrew explains.
“It has given us a real opportunity to expand our hay and straw business without sacrificing the quality of the product.”
He admits that the cost of an accumulator can put off some operators, but believes that his experience shows the machine’s value.
“The initial price might be a shock, but we ran our first for 10 years with only negligible maintenance issues, and when balanced against the added labour required to move bales with a flat-eight and additional labour, it really does stack up.”
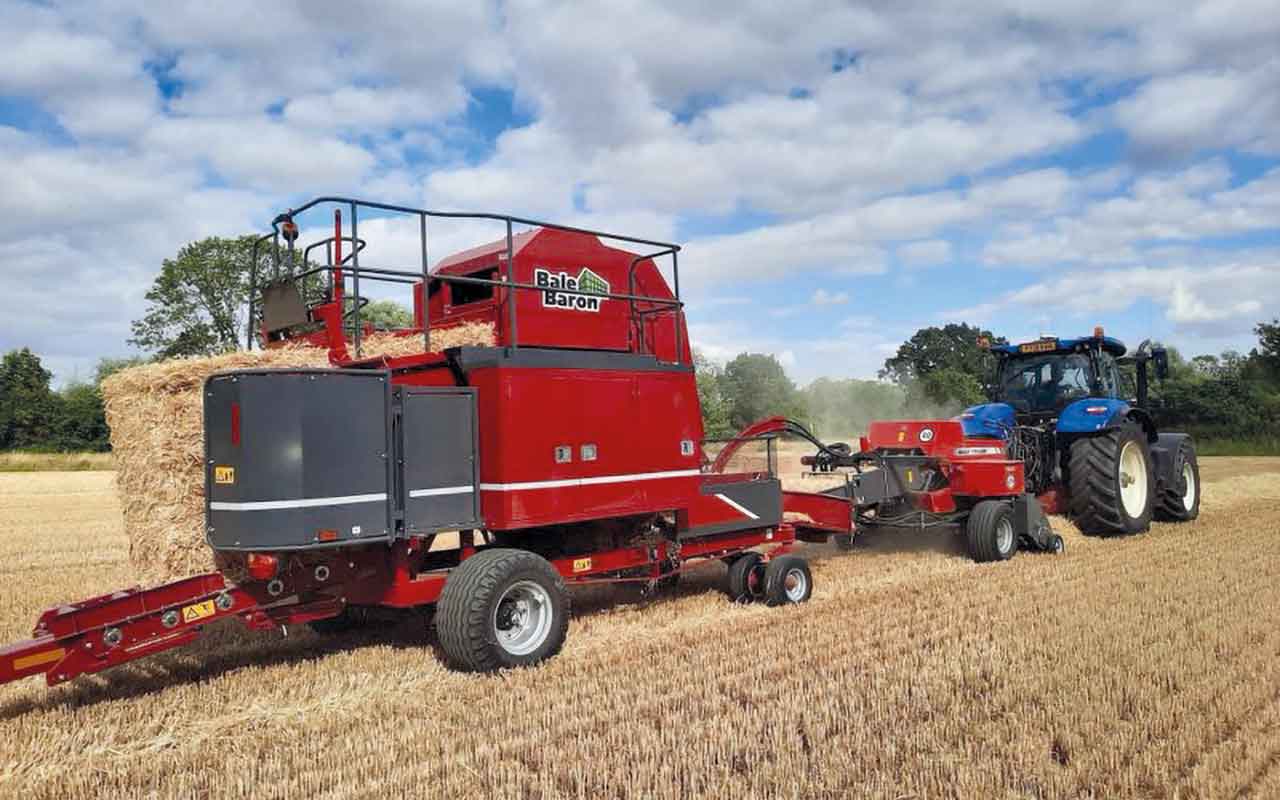
Bale Baron
Winner of the 2022 Contractor of the Year award, Tim Russon had just completed his first season with a Bale Baron 4250 trail-behind machine the last time we visited.
This had replaced a Bale Bandit accumulator, which Tim believes was no longer able to keep up with the expanded hay and straw area, and which was complicated to use.
“The Bale Bandit could just about handle 30,000 bales a year, and it caused some problems with the steel bands,” he says. “They were difficult to dispose of, whereas the Bale Baron just uses string.”
This year, Tim added a second 4250 to the fleet, along with two Massey Ferguson 1840 in-line balers, both fitted with the Weighay system.
“Having this combination has helped maximise the weight of the bales without affecting their length. Each bale has increased from 14.5kg to 19kg, meaning every lorry load has about 4.5t more.”
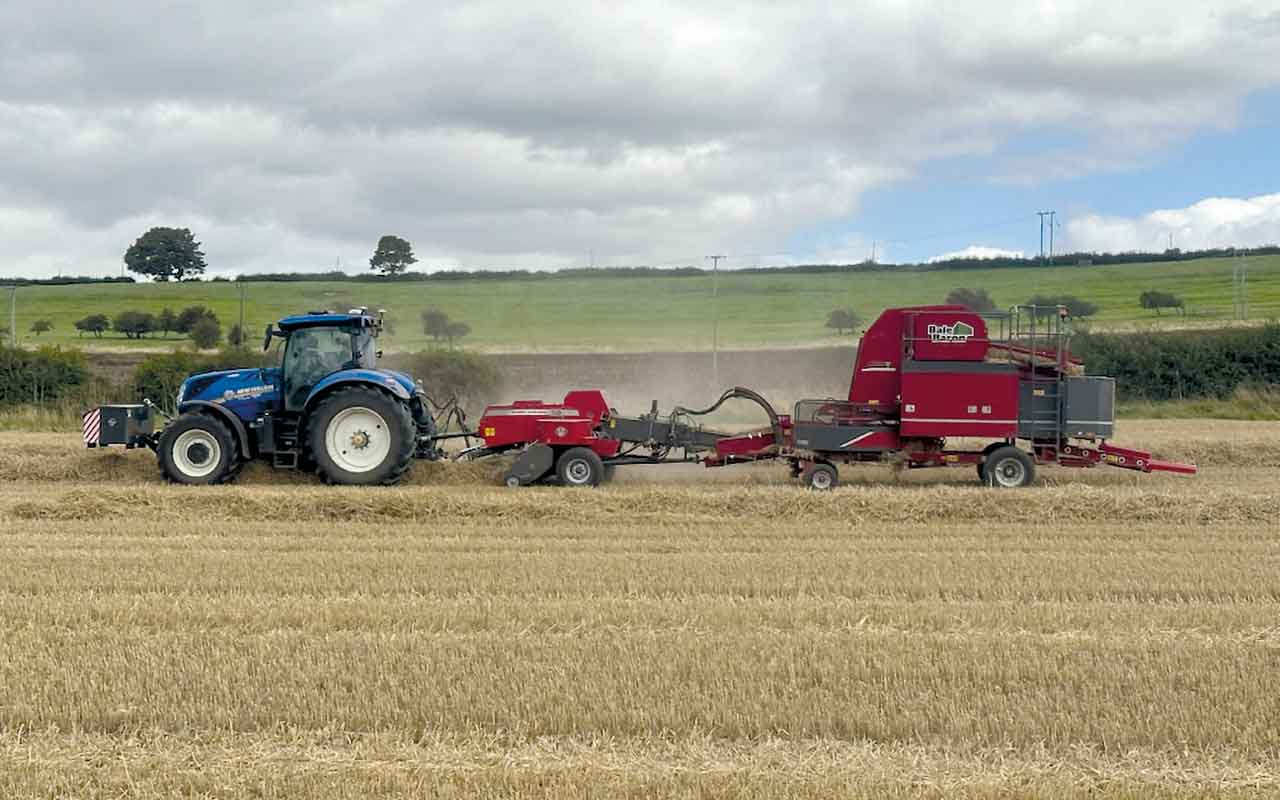
Keep things moving
He says the second Bale Baron took out the risk of producing conventional bales.
“We’d gotten up to 75,000 bales of hay and straw a year and wanted to expand further, but the tight weather windows meant one machine would struggle with that.”
The efficiencies start in the field with the packs of 21 conventional bales. Tim can pick up three of these with the loader, meaning that 63 bales can be loaded on the trailer in one movement – far above what would be possible with previous options.
This also speeds up the unloading process at the farm, and the reloading when straw merchants come to collect.
If the bales are a consistent size, Tim says the Bale Baron is very easy to use as well, following directly behind the balers and able to handle even high-yielding crops.
The company also offers a pick-up model, which can be used independently of the baler. The machine is hydraulically powered, with Isobus compatibility as standard, meaning that any adjustments can be made from the cabin.
Power requirement
While putting an additional machine behind the baler might seem like a quick way to increase the power requirement, the Bale Baron only needs about 100hp and a minimum of 95 litres/min hydraulic flow, meaning most tractors can handle the conventional baler and Bale Baron, depending on the topography of the fields.
“More importantly, it means I can be confident that everything we bale will be in the shed by the end of the day. There’s no chance of bales getting damp and musty.”
With the addition of a second machine, Tim hopes to continue developing the hay and straw business by taking on more contract baling and potentially more ground to build on the bale sales.
“We’re getting close to 100,000 bales a year, which the two machines can easily handle. I would hope we can get to between 120,000 and 130,000 without any problems.”