Concerns over erosion in maize, as well as the cost of inputs in all crops, have led to flagship planters being fitted with precision features to ensure optimum plant spacing and fertilisation.
Amazone
The trailed Precea-TCC is based on the PreTeC sowing unit. Singling discs are driven individually via the ElectricDrive system, providing infinitely variable seed spacing and individual row shut-off as standard.
Up to 350kg coulter pressure per PreTeC sowing unit is available, increasing for the coulters behind the wheels. The SmartForce active coulter pressure system senses the resistance from the soil and adjusts the downforce to maintain the desired planting depth.
The seed is delivered to the singling disc from a choice of individual 70-litre hoppers (6000-TCC only) or using the Central Seed Supply (CSS) system.
The fertiliser hopper consists of one 3,000-litre tank on the 6m or two 3,000-litre units for the 9m and 12m. Fertiliser is supplied down to the FerTeC HD double-disc fertiliser coulter via the FertiSpot portioner.
This collection of the fertiliser as a deposit means the rate can be cut by 25% with no effect on yield, according to the company.
The drills also feature CurveControl, which speeds up the outer units to ensure the seed spacing is kept the same as the inner rows, which are going slower.
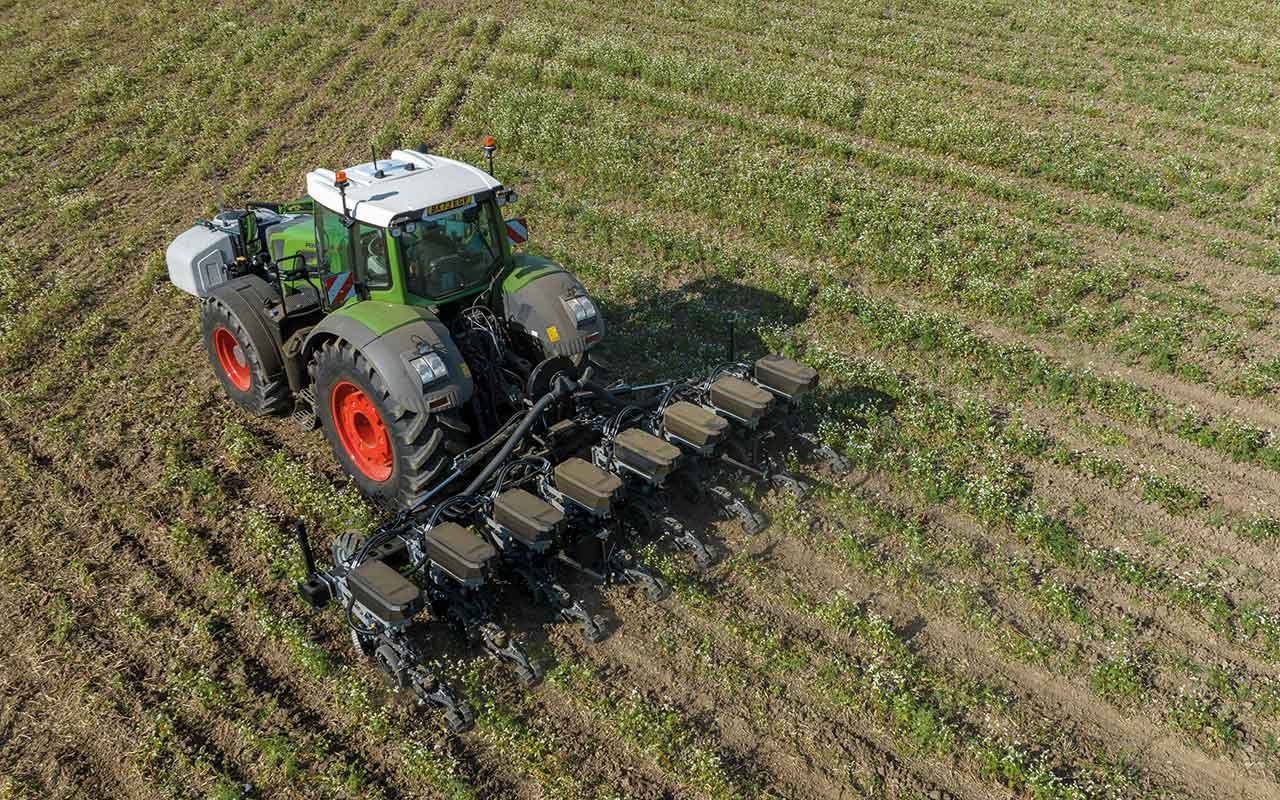
Horizon Agricultural Machinery
Horizon says more farmers are seeking to cut soil disturbance before planting. Because of this, development has been focused on a new generation of planters that must perform across various field conditions, from fully cultivated to no-till soils.
Available in folding or rigid configurations up to 7.5m wide, with row spacings from 35cm, the PPX supports numerous options.
It can be configured with a frame-mounted liquid fertiliser tank or granular hopper and pairs easily with an FT2200 or third-party front tank.
Mounted on a sliding toolbar for adjustable working widths, its row units attach individually via parallelograms with 33cm of travel, ensuring consistent depth control and soil contact.
These parallelograms are extremely stiff, featuring hardened steel machined pivots for reliable performance, even in the toughest conditions.
The PPX integrates precision planting tech from the factory. These systems, also available as retrofit upgrades on major brands, allow operators to create a bespoke planting solution, according to the company.
Available features and options include automated downforce control, pneumatic row cleaners operated from inside the cab, and FurrowForce, an adaptive two-stage closing system.
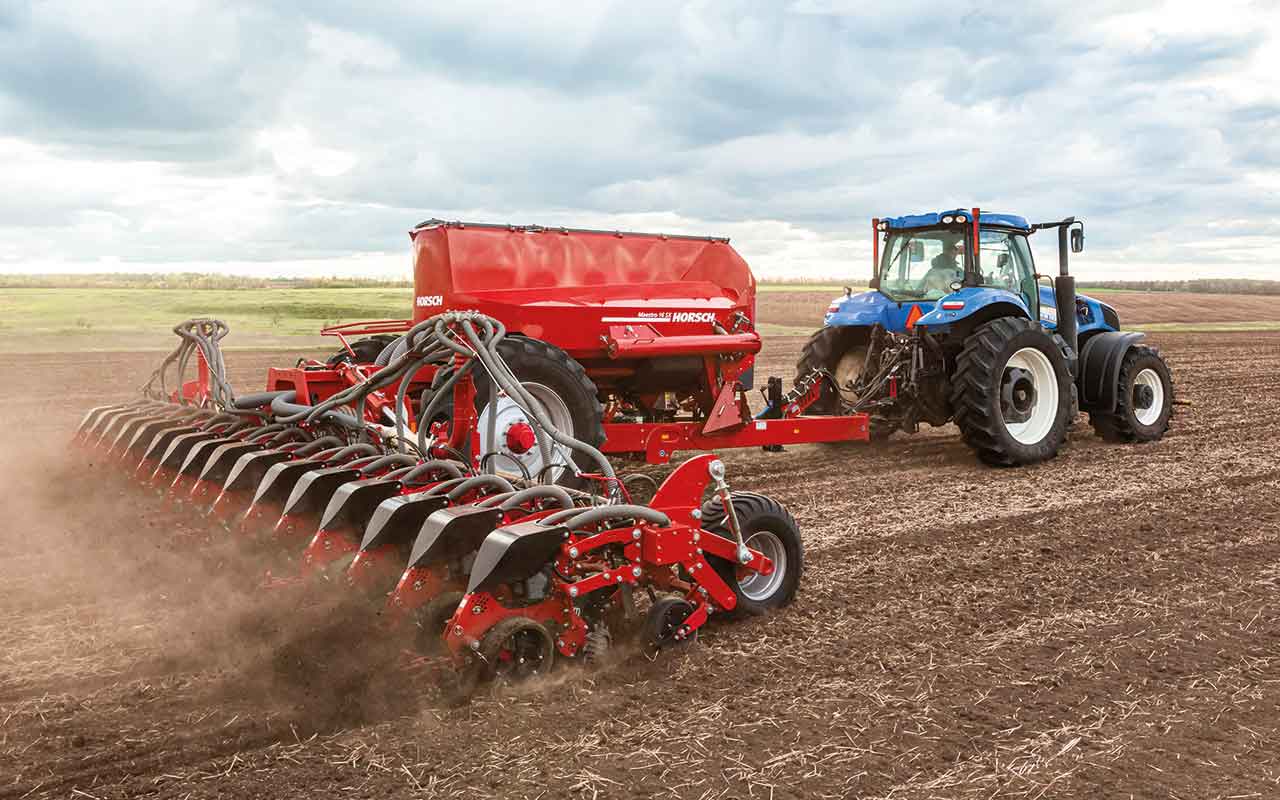
Horsch
The Maestro SV/SX is the second generation of the most successful Horsch planter and is offered with a working width of 9m or 12m.
Two different seed wagon sizes can be used with the Maestro SV/SX. The standard version of the central pressurised double hopper has a capacity of 2,200 litres for seed and 5,400 litres for fertiliser.
An optional 50:50 partition of the hopper is used to sow a lot of legumes.
Both are equipped with the central tank system MTS. It meters product pneumatically from the seed wagon. Fertiliser is applied conventionally via single- or double-disc fertiliser coulters.
The seed is transported to the rows and singulated with AirVac or AirSpeed.
The Maestro row unit is equipped with a wide, stable parallelogram with a hydraulic cylinder to generate coulter pressure up to 350kg/row. This can be adjusted manually at the terminal or automatically with the AutoForce pressure regulation.
The scraper does not need to be adjusted or changed between crops, requiring only the correct metering disc and therefore reducing seed handling.
A grain sensor provides information about the singulation accuracy and, as both systems are driven electrically, technologies like SectionControl and VariableRate are available.
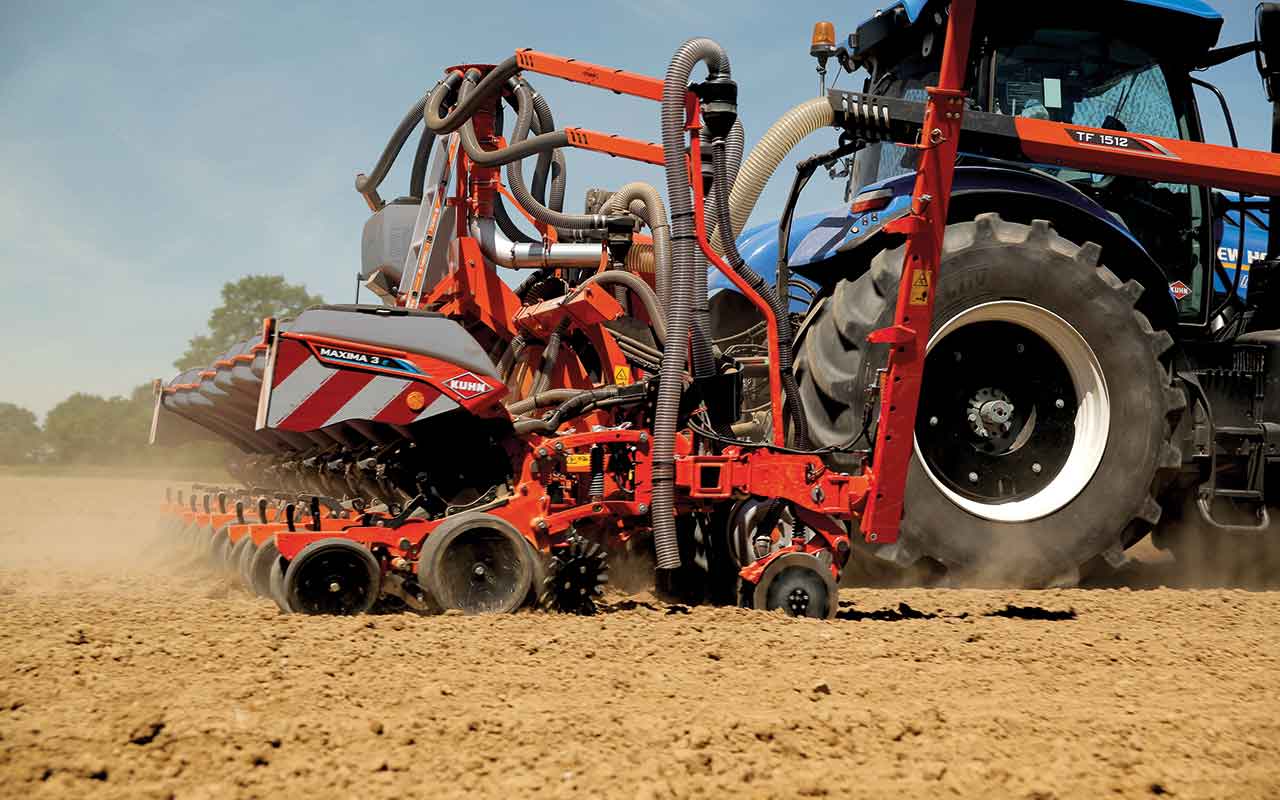
Kuhn Farm Machinery
Electric drive, hydraulic coulter pressure and flexibility to adjust row widths are key options on the Maxima TI L e precision drill.
A new hydraulic coulter pressure option allows a constant pressure, regardless of conditions, to ensure seed is always placed at accurate depths for even emergence.
The 180kg max pressure can be adjusted via Isobus in 5% increments for all soil conditions. This feature also allows users to lock individual rows out of work.
Further flexibility is offered by the telescopic variable row widths. Available in six or seven rows, the frames allow operators to choose spacings between 45cm and 80cm.
The spacings can be changed in about 20 minutes without the need for additional tools.
Electric drive is an option allowing users to adjust seed rate from the cab and control individual row shut-off.
This helps to reduce seed overlap and eliminates any overseeding caused by tractor wheel slip. It is powered by its own 48V system to avoid any signal interruptions, and ensure accuracy when accelerating and slowing down, with curve compensation for headland bends.
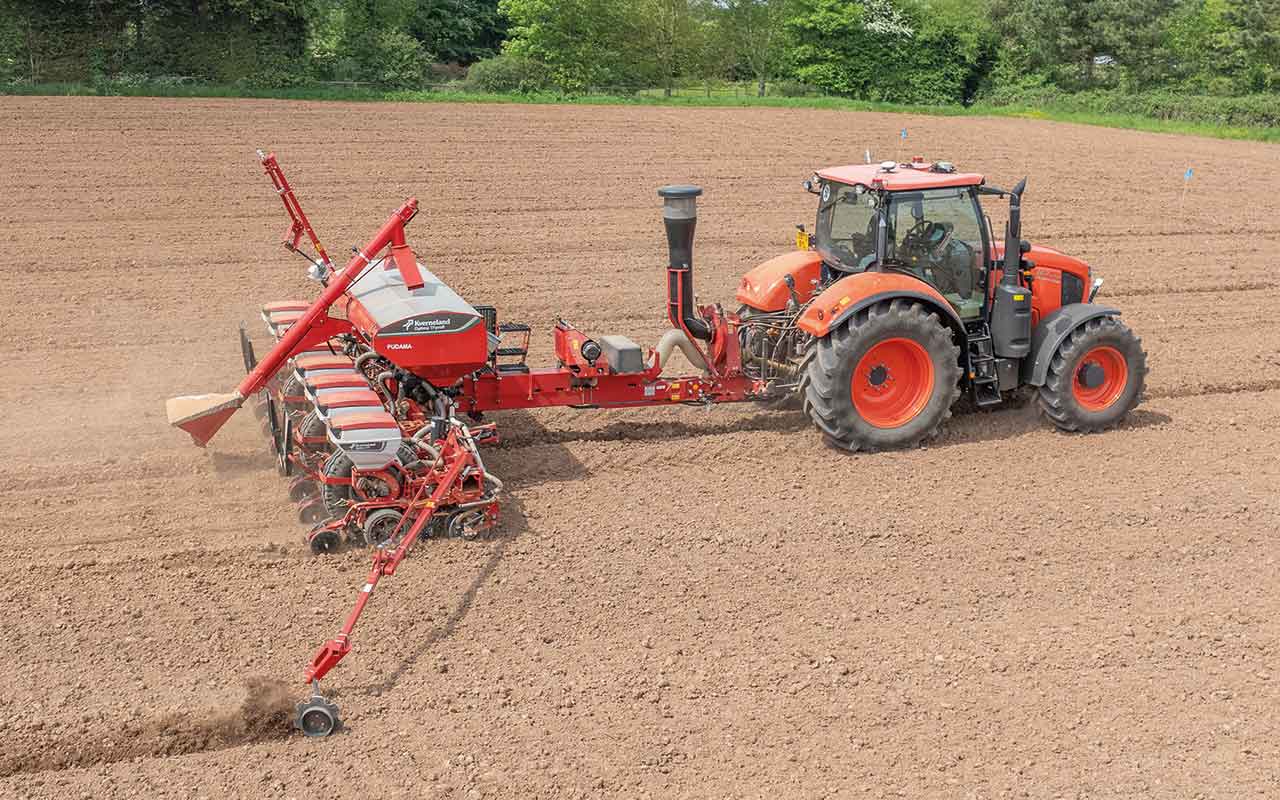
Kverneland
Available on the Optima F maize drill fitted with the SX sowing units, the Pudama system places a defined amount of fertiliser beneath each seed, enabling the roots to easily access nutrients.
According to the company, using the Pudama system can save about 25% in fertiliser without affecting yield or operating speed.
Optima planters are offered with E-drive II, providing individual electric drive to the sowing units, allowing infinitely adjustable seeding distances, controlled through the Isobus terminal.
When using close row spacings (37.5cm) the system can also perform individual tramline switching to adapt to any sprayer width.
E-drive II allows Geoseed to be installed, which synchronises seed placement across the full field. Various specification levels are available depending on the model, and RTK is required.
For beet crops, the Monopill is offered with the E-drive II system, with up to 24 rows on a rigid toolbar and 18 rows on a hydraulically folding frame.
Seed spacing can be infinitely adjusted between 12.5cm and 25cm to ensure crop population matches soil type and conditions; similarly, populations can be increased in rows adjacent to tramlines.
Half-width shut-off and individual row shut-off can also be used to ensure accuracy in fields of all shapes and sizes.
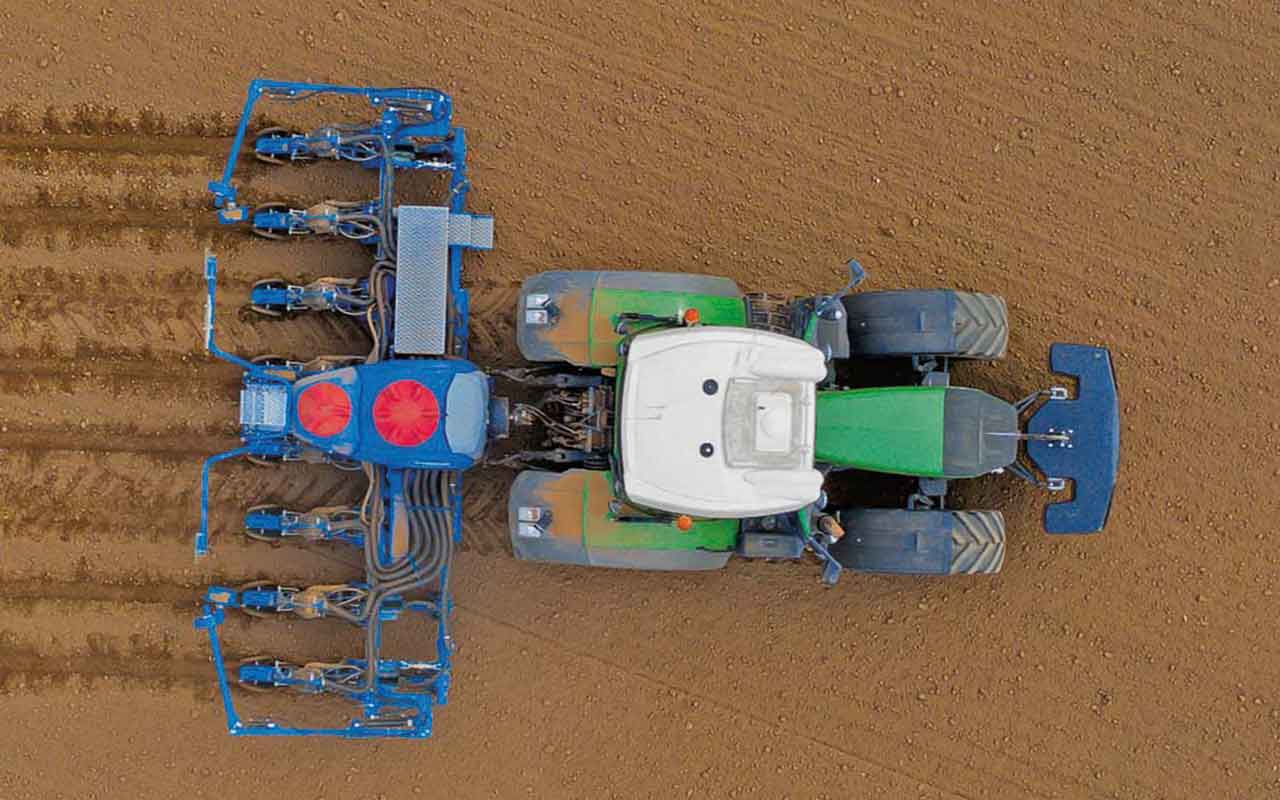
Lemken
The Lemken Azurit 10 places seed in a triangular pattern, rather than a straight line. According to the company, this DeltaRow pattern offers improved distribution of the plants in the field and ensures better use of resources, leading to higher yields.
Fertiliser is placed in the DeltaRow in the root zone. On sites at risk of erosion, the method offers a clear advantage compared to single rows, thanks to more intensive rooting of the soil and improved plant spacing.
In the first work step, clearing stars remove stones, clods and harvest residues from the seed furrow. These can be adjusted in height or removed completely if required.
Once the seed furrow has been cleared, mineral or liquid fertiliser is placed centrally underneath the DeltaRow using a fertiliser coulter with up to 250kg pressure.
Two double-disc coulters place the seed precisely on the reconsolidated soil in the DeltaRow formation.
The seed is conveyed from the singling unit via a shot channel to the seed groove by the existing overpressure.
The seed groove is formed by double-disc coulters. Their outer disc is set at an angle, while the inner disc runs straight along the soil wedge of the trapeze packer roller.
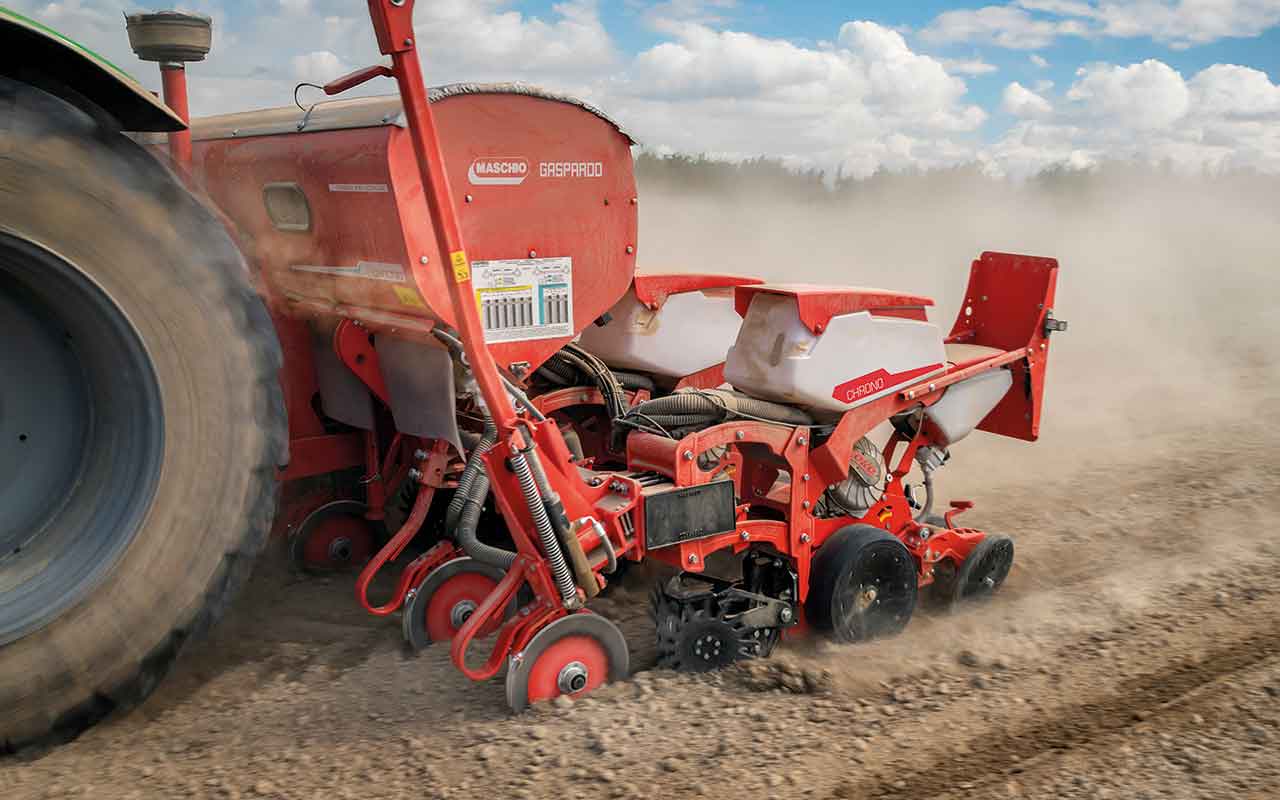
Maschio Gaspardo
Said to offer a working speed of 15kph, the Chrono from Maschio Gaspardo uses an air spring on each planting unit, with an in-cab adjustable ground pressure of up to 300kg.
Metering of the seed and singulation is split within the Chrono system, with a vacuum forcing the seed into the metering disc using an adjustable force based on the seed dimensions.
After this, the system is pressurised to push the seed down to the coulter, with adjustable pressure based on the working speed and planting depth.
The distributor is tilted to 15deg to ensure a straight pipe down to the coulter, to minimise blockages.
The Chrono has a fully electric transmission for full adjustability across the system. Sitting at the top of the range is the 800 and 900 ranges, both with a central hopper that can be split for seed and fertiliser.
When fertiliser application is specified, this is sent down to a single-disc coulter from the central tank. When the central tank is seed only, the unit hoppers can be used for microgranules.
The 800 is available with 12 or 16 rows, for spacings from 70-80cm, while the 900 can be fitted with up to 24 rows. Full Isobus compatibility is available, for both variable-rate and section control functionality.
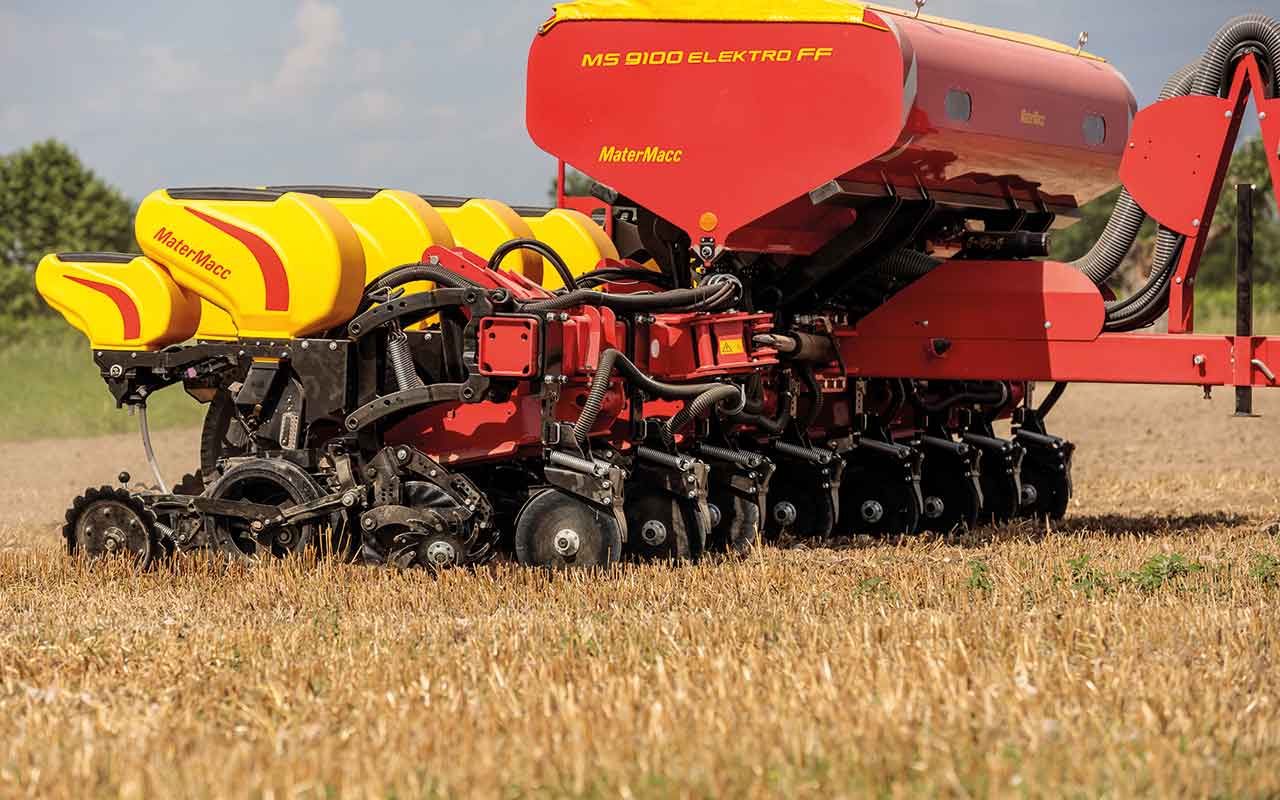
MaterMacc
Part of the Pöttinger Group since 2022, MaterMacc is an Italian firm specialising in the design and production of precision pneumatic seeders.
The MS 9100 precision planter is characterised by a front folding frame with sequentially operated wheel supports and telescopic drawbar.
All the movements are hydraulic and managed by electronic valves with sensors for an easy folding-unfolding sequence.
The foldable frame is made from a 180mm square section and is suitable for 70cm and 75cm row spacing, with a working width of 6m and transport width of 3m.
The planting unit can produce up to 250kg of downforce when needed, while the Magicsem Plus metering unit is made of a special blend of polymers and fibreglass said to provide great torsion and flexural strength.
The agitation inside the loading chamber improves seed drawdown, even at high speeds, while protecting seed integrity and without limiting the range of distributable crops.
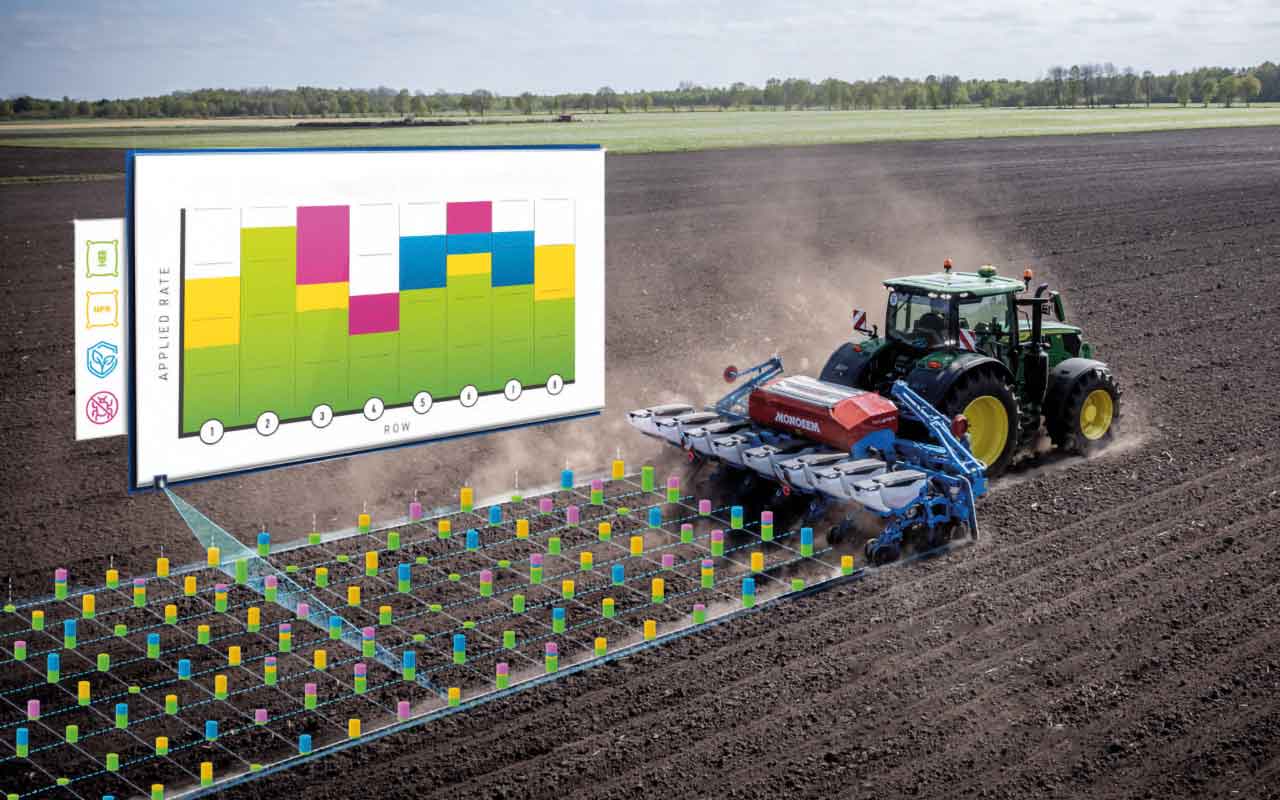
Monosem
Distributed in the UK by Toucan Farm Machinery, Monosem machines have been updated with QuadRate Pro.
According to the company, this represents a significant advancement, offering the ability to modulate row-by-row application for seed, fertiliser and micro-granules simultaneously.
It uses a new 56V architecture, developed specifically for the ValoTerra range to handle row-by-row dosing, capable of running up to 32 motors individually across an eight-row planter. For greater accuracy, up to four modulation maps can be used at once to guarantee precision.
It is operated through the new SeedStar M Isobus software and is said to offer a unique combination of features to reduce the use of inputs. This technology makes it possible to cut seed density in low-yielding areas while minimising the use of fertilisers and phytosanitary products.
Optimising inputs maximises the potential of each land while promoting optimal growing conditions for crops, thereby increasing profitability.
Additionally, QuadRate Pro simplifies product application with direct import of ready-to-plant modulation maps. This guarantees high precision for sowing, accessible to all operators.
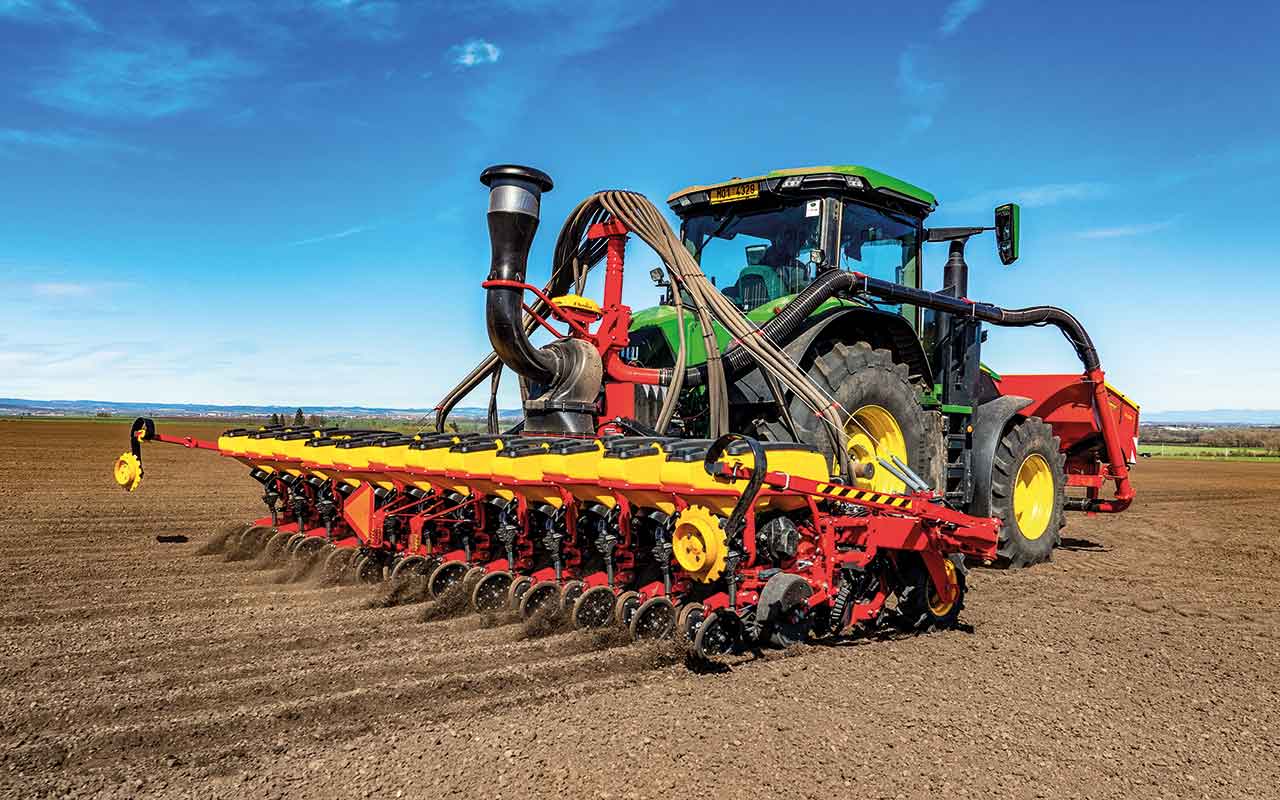
Väderstad
By upgrading the data processing capabilities of the Tempo F, Tempo V and Tempo L, Väderstad has enabled extra precision-enhancing features to be unlocked.
These optional features include auto- singulation, curve compensation and active hydraulic downforce.
The optional electronic WSX system further boosts performance, with auto-singulation as a key advantage.
Sensors in each row unit monitor and automatically adjust seed singulation to the optimal setting, saving time and increasing productivity – especially valuable for farmers and contractors who frequently switch crops.
Additionally, the active hydraulic downforce system allows the driver to set an optimal row unit pressure, which is maintained automatically.
According to the company, the Tempo instantly reacts to changing soil conditions, ensuring consistent planting depth despite variations in soil type or compaction. This guarantees uniform conditions for all seeds, maximising their growth potential.
Finally, curve compensation is achieved through advanced gyro sensors, which detect when the machine is turning and adjust the metering output of each row unit accordingly.
This ensures a consistent seed rate across the full planter width, maintaining accuracy even in curved field sections.
Tempo models with up to 32 rows are available, with individual row unit hoppers or a central fill system to suit requirements.