Many of the updates have been focused on two things: the integration of film-on-film wrapping and greater automation of the baling and wrapping process.
The benefits of film-on-film are well known, as it means only film plastic must be purchased for the operation. This makes a significant difference when unwrapping the bales, as the waste does not need to be sorted and can be recycled together.
For automation, Isobus machines have started integrating tractor implement management (TIM) functionality. Round baling is a stop-start operation, unless you’ve opted for a non-stop variant.
You stop when the chamber is full so the net or film can be applied, and the bale can be ejected. TIM automates the stopping and starting, as well as several other functions, to enable the operator to focus on the feed-in of the baler.
Case IH
The Case IH RB545-series fixed-chamber comes in standalone or Silage Pack format equipped with an integral wrapper. Updated for the 2024 season, both have a 2.3m double cam-track pick-up for handling heavy swaths and a 20-knife chopping unit.
High-density bales are produced via 18 rollers, with a new profile said to improve bale rotation, and are mounted on automatically greased bearings.
On Silage Pack models with either 1,000rpm or 540rpm PTO drive specifications, the main gearbox has been tilted upward by 3.5deg for better shaft alignment to maximise durability.
These also benefit from the addition of a deflector in the bale transfer area to prevent crop accumulation and any need to spend time on removal.
Component durability has been enhanced by greaseable bushings on the tailgate locks and bushings for the drop floor pivot arms on both standard and Silage Pack models, plus improved sealing for the conveyor cylinder to prevent water ingress and protect the integral position sensor.
Silage Pack versions also feature an improved bale quarter-turn system, with a higher-strength gas strut to decrease the manual handling force required while folding from field to road position.
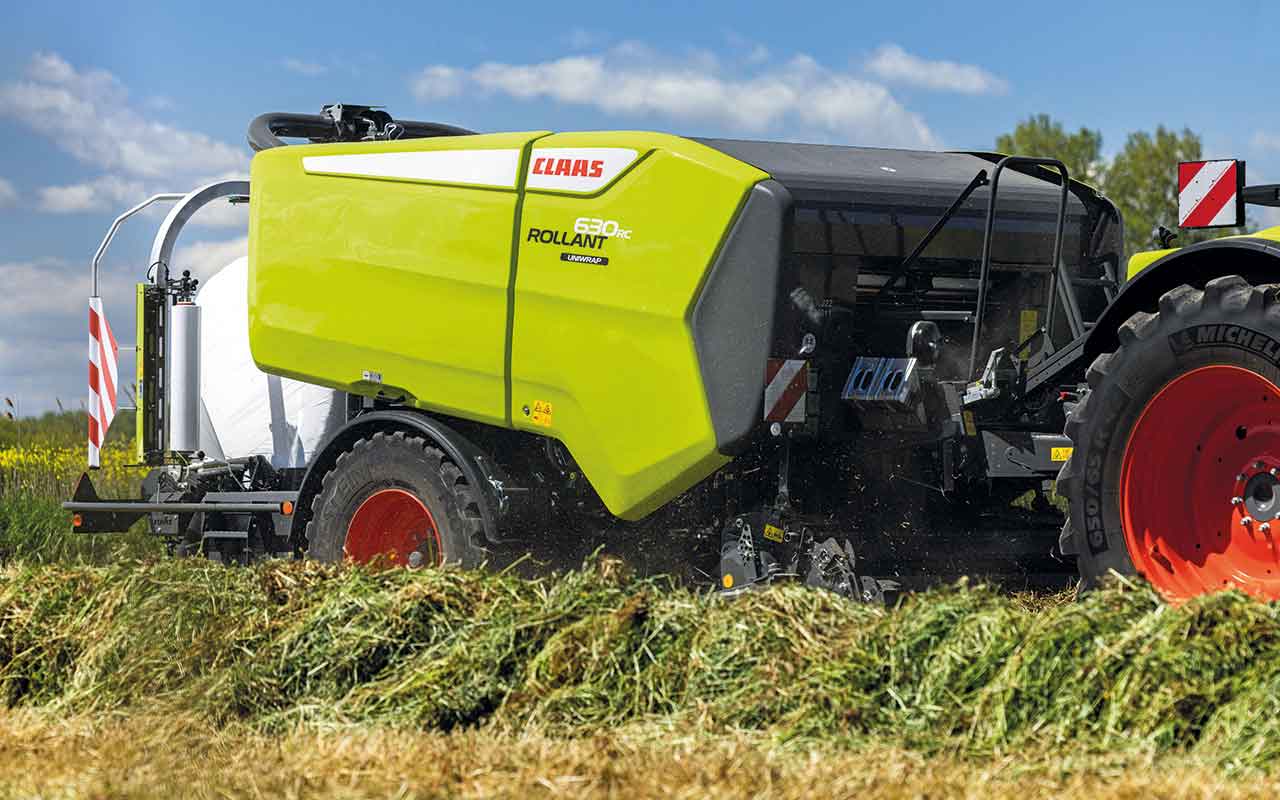
Claas
The Rollant 630 RC Uniwrap is the first model in the range to feature the Y-shaped design introduced in the Lexion in 2019, and comes with a host of new features.
The latest Claas Multiflow pick-up offers a 2.1m working width, with five cam-controlled tine bars as standard. The new cam-trac is said to reduce the power requirement by 20%.
Crop is transferred to the Roto Cut cutting rotor with double boron tines arranged in a helical formation, with the option of a 25-knife cutter bar with a possible 44mm cut length.
The new central lubrication system can be further upgraded to include greasing of the complete wrapping table.
The 1.25×1.2m chamber works with 16 steel rollers with a ribbed profile. The thickness of the drive shafts has been increased in areas subject to heavy wear, enabling higher bale densities and weights to be absorbed.
The machine can be supplied with the Maximum Pressure System Plus. The pivoting three-roller segment in the tailgate delivers extra pressure.
At the start of the baling process, the rollers project into the chamber. These are then pushed up into their end position by the bale as it increases in size.
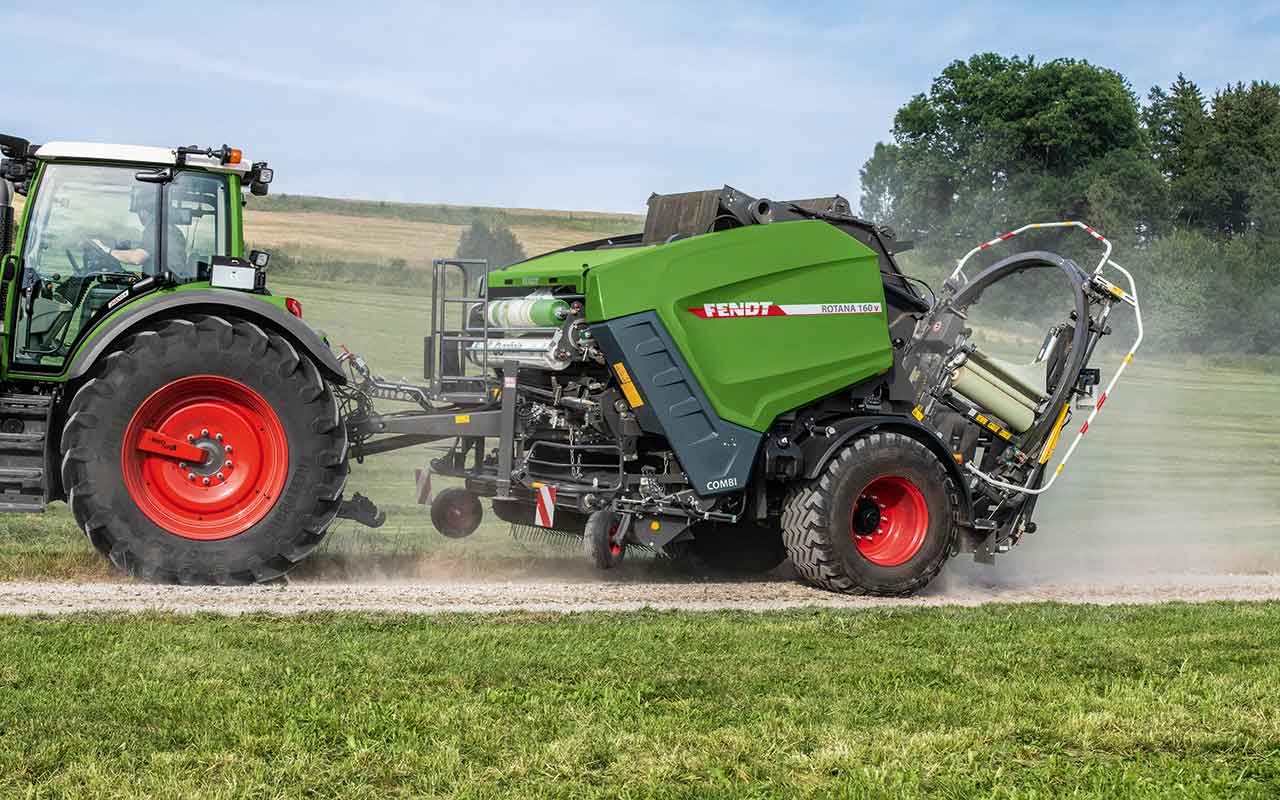
Fendt
Last year, Fendt introduced a series of optional feature for its Rotana Combi balers such as moisture analysis and weighing function in future.
These automated features are packaged into Fendt Load-sensing Profi and Fendt tractor implement manager (TIM) Profi.
With the Profi function package, customers can now access direct parameters such as bale-specific weight and moisture. As a result, round bales can be planned into the stock feed plan or marketed according to their average dry matter content.
Two sensors on the inside wall of the chamber measure the moisture of the bale as it is formed. The upper limit for moisture can be adjusted from the cab, and if this is exceeded for more than three seconds, an acoustic signal sounds.
The company says data collected can also be used to optimise future operations. The Rotana saves field-specific data in Fendt Task Doc.
This means the dry matter harvested can be determined and used to plan rations, as well as fertiliser requirements for the next cut, or the field in general.
Automated bale ejection is standard. For TIM-capable tractors, the TIM Auto Stop function stops the tractor when the bale reaches its target size and density.
After this, the bale is tied, transferred, wrapped and deposited without user intervention. Once the bale is on the wrapping table, the operator simply activates the joystick to continue moving.
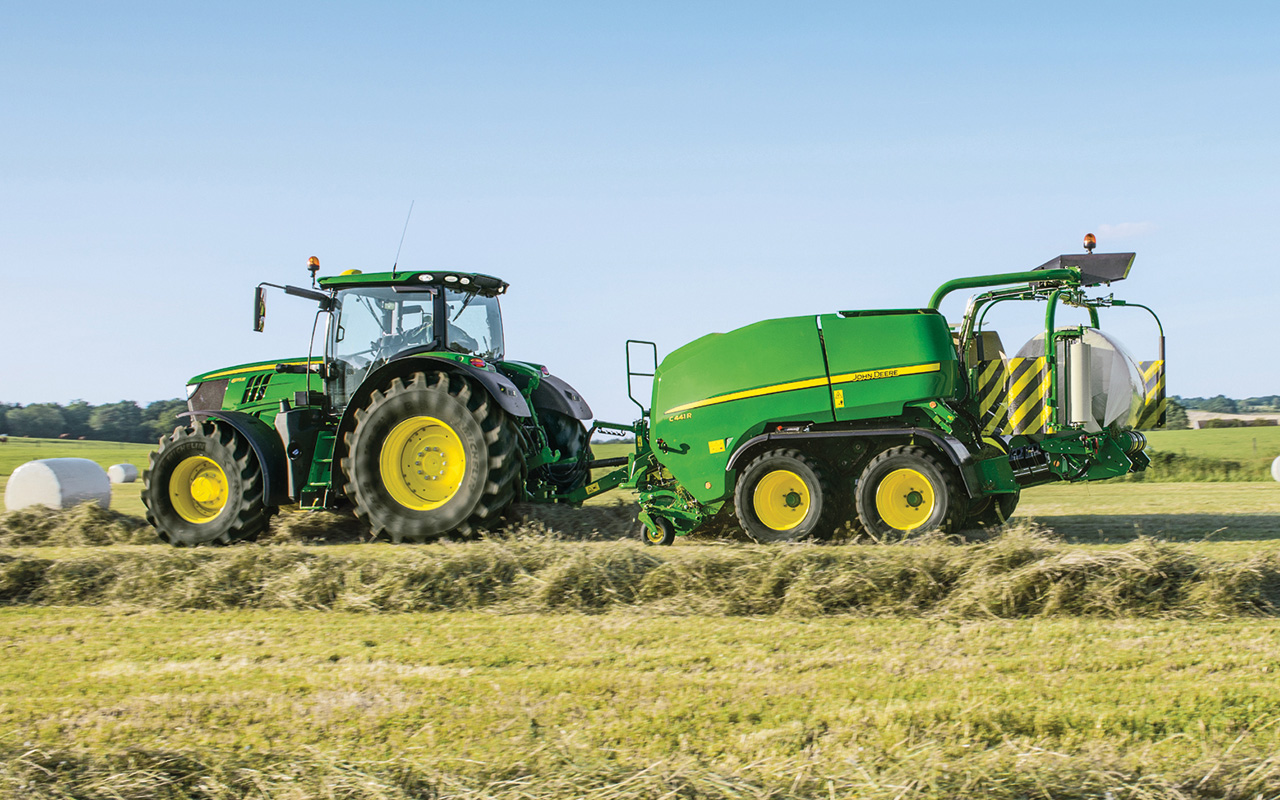
John Deere
Developed to meet the high-capacity requirements of contractors and larger livestock farms, John Deere’s C441R combi-baler incorporates a heavy-duty drive system rated at up to 210hp with a 1,000rpm PTO.
The 18-roller bale chamber has a 121cm width, and a transport table system allows one bale to be held while the next bale is being formed before ejecting both at the same time.
This saves time, simplifies bale collection logistics and accelerates harvesting. The company says the wrapping system is fast, with the arm moving at 40rpm.
Film-on-film wrapping is available, giving a firmer bale shape and simplifying materials buying and plastics disposal once the bale is unwrapped.
John Deere claims that the C441R is an all-rounder, capable in both heavy, wet grass crops and dry straw, producing bales with consistent density and shape in all crop types.
Operators can choose from 2m or optional 2.2m pick-ups, feeding a high-capacity MaxiCut HC rotor with 13 or 25 knives.
The baler also incorporates a full-width parallel drop-floor system operated from the tractor cab, which enables blockages to be removed instantly.
The machine is available with a single axle as standard or with an optional tandem-axle chassis for improved stability.
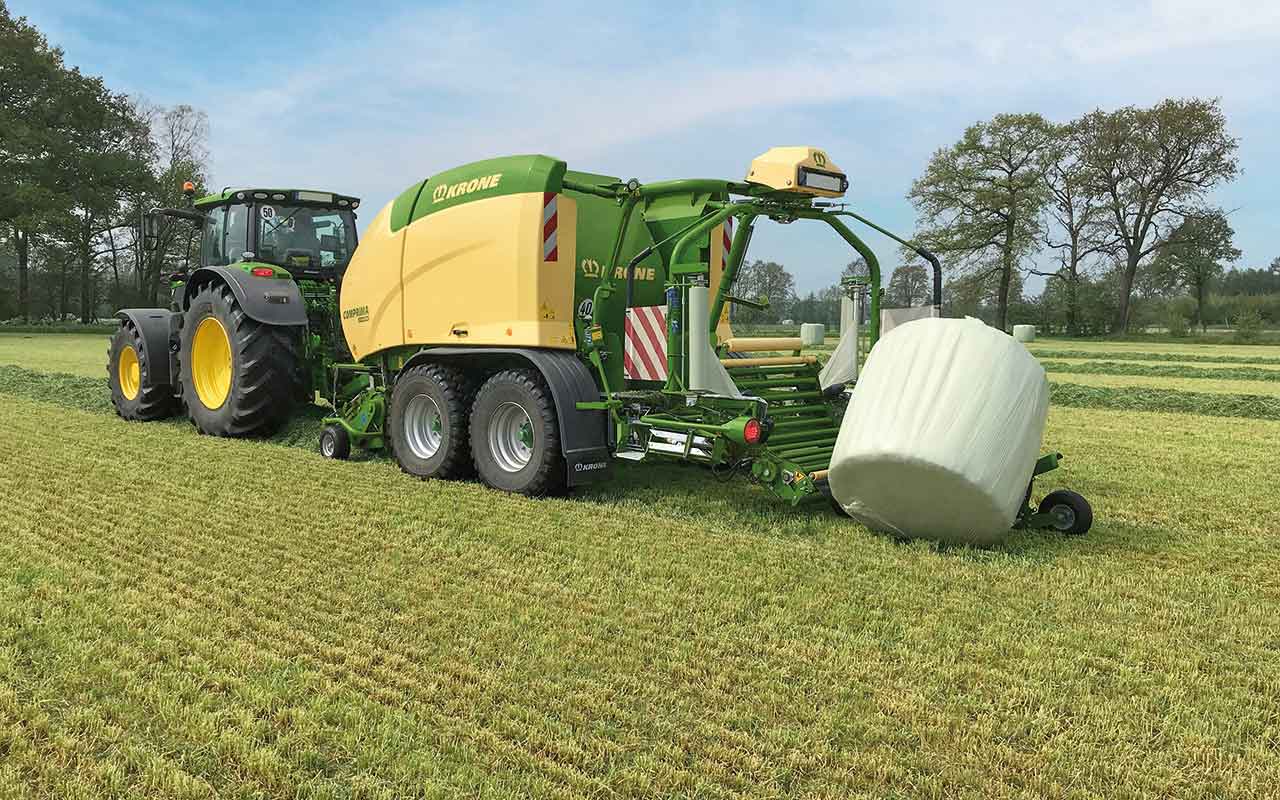
Krone
Krone’s Comprima CV 150 XC Plus has a variable chamber suitable for bales from 1m up to 1.5m, with NovoGrip technology that uses slats and fabric belts, instead of rollers, to rotate the crop and form a high-density bale.
The company claims this system is less noisy than others on the market, service-free and lighter, which reduces the power requirement.
Film-on-film technology is available as an option, as is tractor implement manager to enable the baler to control the stop and start of the tractor, limiting operator input to reduce fatigue and provide consistent bales across the field.
At the front of the machine, the EasyFlow pick-up pivots sideways and can reportedly handle the most difficult conditions at high work rates.
More than that, its rugged build, with very few moving parts, provides a dependable performance. This feeds into a 530mm Hardox rotor, with the option of a 17- or 26-knife chopping unit.
The machine is mounted on a tandem chassis as standard, minimising compaction across the field and improving stability, even in hilly conditions.
At the rear of the machine, the twin-arm wrapping table is designed to offer a wide overlap to ensure full coverage, with controlled blades for a clean cut of the film.
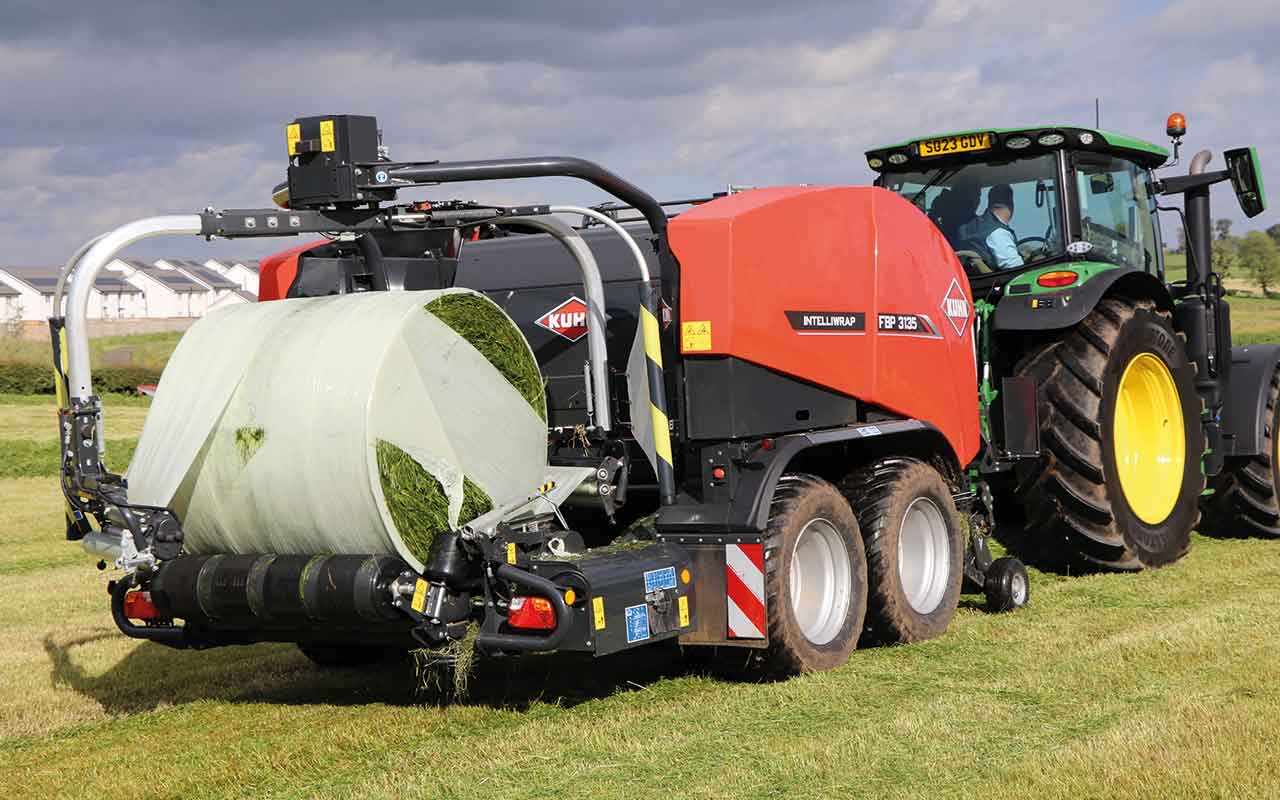
Kuhn Farm Machinery
Following the launch of the VBP 3200 range in 2023, Kuhn has introduced several updates to models across its combination balers to improve wrapping efficiencies and field logistics.
3D Eco wrapping has been added to the FBP fixed-chamber and the VBP variable-chamber combination machines to improve wrap delivery on the bale. It produces tightly sealed bales that are said to hold their shape better.
The system applies the film where it is most required – to the bale shoulders that are prone to damage – and reduces film application to the less-vulnerable middle section of the bale’s circumference.
The cylindrical wrap also expels more air to offer a complete seal and constant shape, even after long storage periods, and the wrapping time is also reduced.
Both the FBP and VBP models can automatically unload bales in pairs to make collection easier. This saves time and fuel when loading and cuts soil compaction from loader movements.
For easier loading of film rolls onto the wrapping units, a hold to run button, situated at the rear of the machine, allows users to rotate the satellite wrapper from the rear to allow loading film from one side, rather than lifting rolls around the machine.
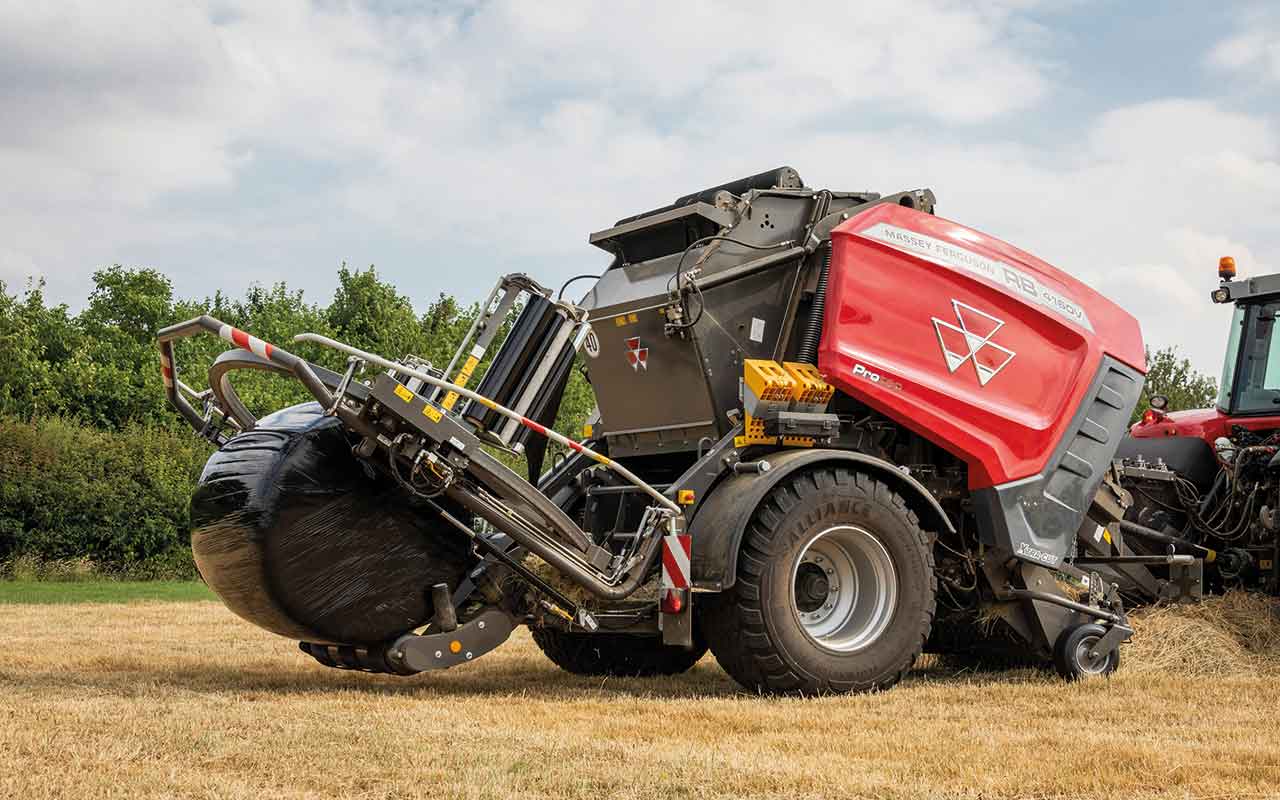
Massey Ferguson
New options this year on the Protec range of baler-wrappers include the option of moisture monitoring, using sensors within the bale chamber to measure this and wirelessly transmit the data to the in-cab terminal.
Additionally, tractor implement manager will be available across the range, automating a series of load-sensing hydraulic features across the baler.
These include automatic pick-up lift at the end of rows; automating the opening and closing of the tailgate; swapping out knife groups and activating the unblocking system.
This can be complemented by moisture monitoring, as well as a bale scale and surface optimiser.
When hooked up to an Isobus tractor, operators won’t need an extra Bale Control terminal, as this information will be integrated into the in-cab display.
Protec balers are available with fixed or variable chambers, offered with net wrapping, or film-on-film technology.
Key points throughout the range include the option of the Xtracut chopping system, with up to 25 knives, as well as the Constant Pressure System, which uses springs and hydraulic tensioning arms to create a high-density core to the bale and then gradually increases the pressure as the outer bale is formed.
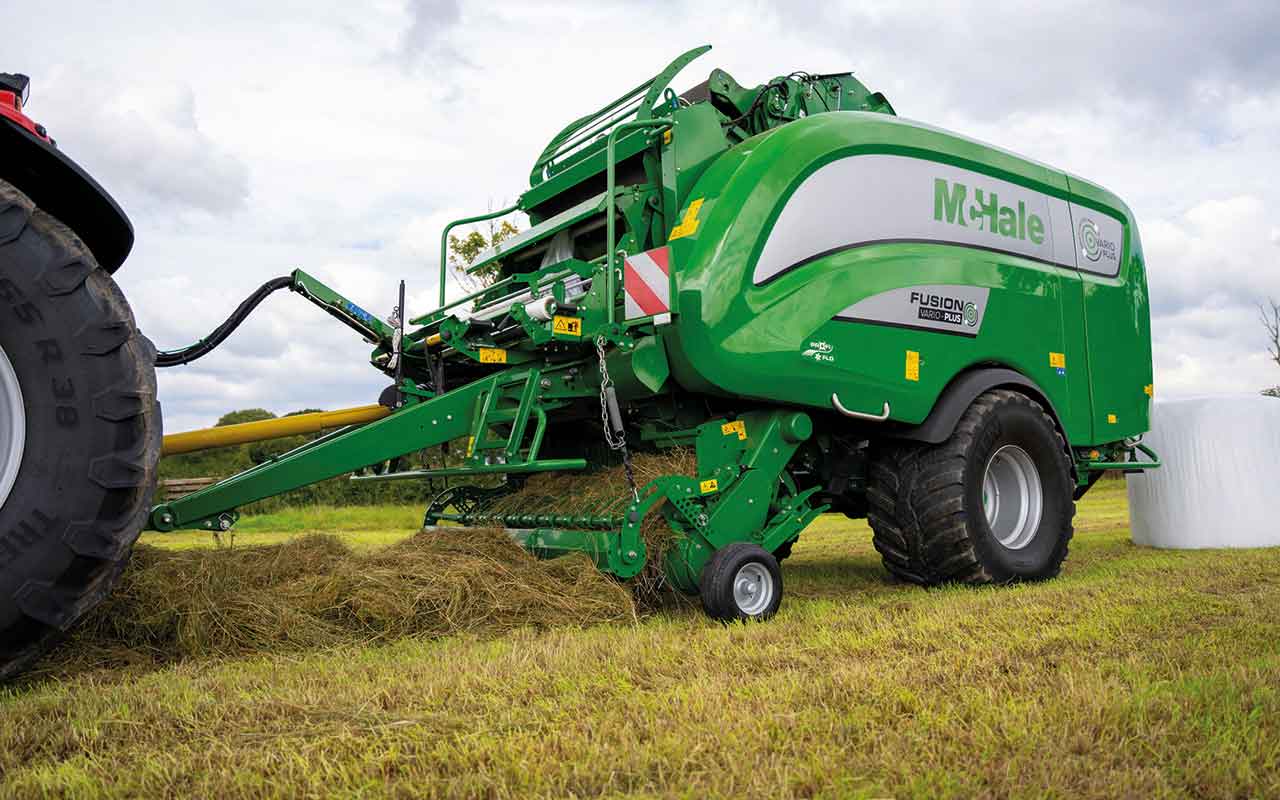
McHale
Said to be McHale’s highest-output pick-up for the Fusion 4 range, the Profi-Flo features a tapered feed channel that encourages the crop to flow from the pick-up towards the rotor and into the bale chamber, maximising throughput.
To reduce maintenance, all Profi-Flo pick-ups are fitted with a heavier driveline which reduces chain load and increases chain life.
Customers can choose between a five-tine bar cam-track pick-up or an optional six-tine bar camless pick-up, which has increased in width.
McHale has also introduced Adaptive Intake, which allows the intake area to automatically adjust up and down to changes in material flow.
Other features on the Fusion 4 range of machines include a larger net/film brake, said to provide 25% more stretch.
Cut-and-hold slider brushes improve reliability by reducing friction to eliminate plastic tearing, particularly in hot or wet conditions.
They also feature a hydraulic tap to lock the cut and hold in the open position for the ease and safety of maintenance.
All machines also feature increased density pressure, which results in the production of a well-shaped and tighter bale.
Optional extras include selectable knives, film/net loading device, side tip, and bale weighing and moisture monitoring.
All McHale Fusion 4 Pro and Fusion 4 Plus machines are Isobus compatible as standard, with the option of an Isobus terminal delivered with the machine.
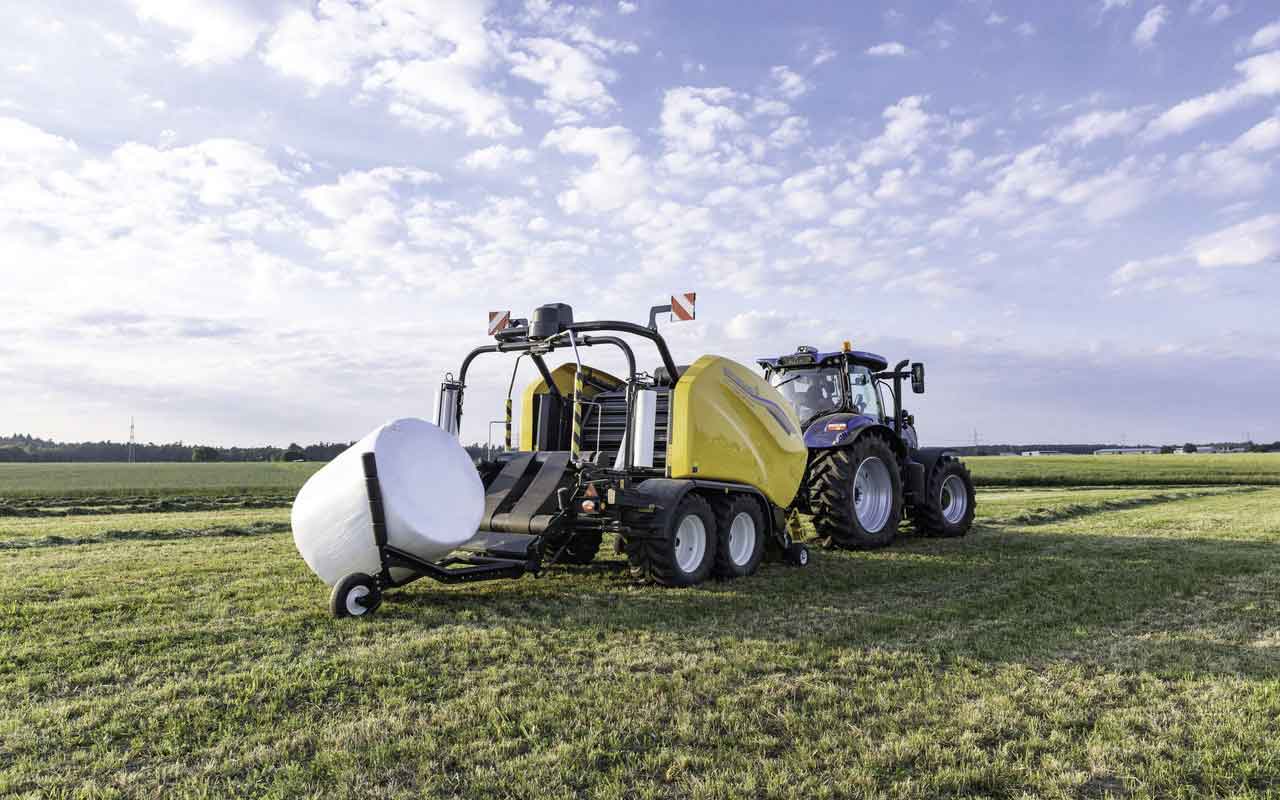
New Holland
New Holland has updated its fixed-chamber Roll Baler 125 standalone and Combi wrapper versions to enhance crop intake, give greater durability and reduce cleaning requirements.
Beneath the refreshed styling, the balers – which produce bales 1.25m high and 1.22m wide from a 2.3m five-bar double-cam pick-up, with 470mm feed rotor, 20-knife CropCutter chopping unit and 18 rollers – now benefit from higher-grade chain drives in key areas such as the intake rotor and bale chamber.
This enhances durability and power delivery in heavy crops and extends its life.
The gearbox angle has been improved to maximise PTO shaft lifetime, and there is now a 1,000rpm PTO option for both standalone and combi models.
To improve crop flow, the 1,200mm-wide Hardox feed rotor, with 10mm finger thickness, has received a scraper to minimise ‘back-feeding’ and help keep down power consumption.
The durability of the dropfloor action has been improved with the addition of a new bushing for the pivot. The company claims workrates on both machines have been boosted by up to 40% faster tailgate opening speed.
The quarter-turn bale deposit function benefits from an update, including a stronger gas strut to ease the manual force needed when changing between work and transport positions.
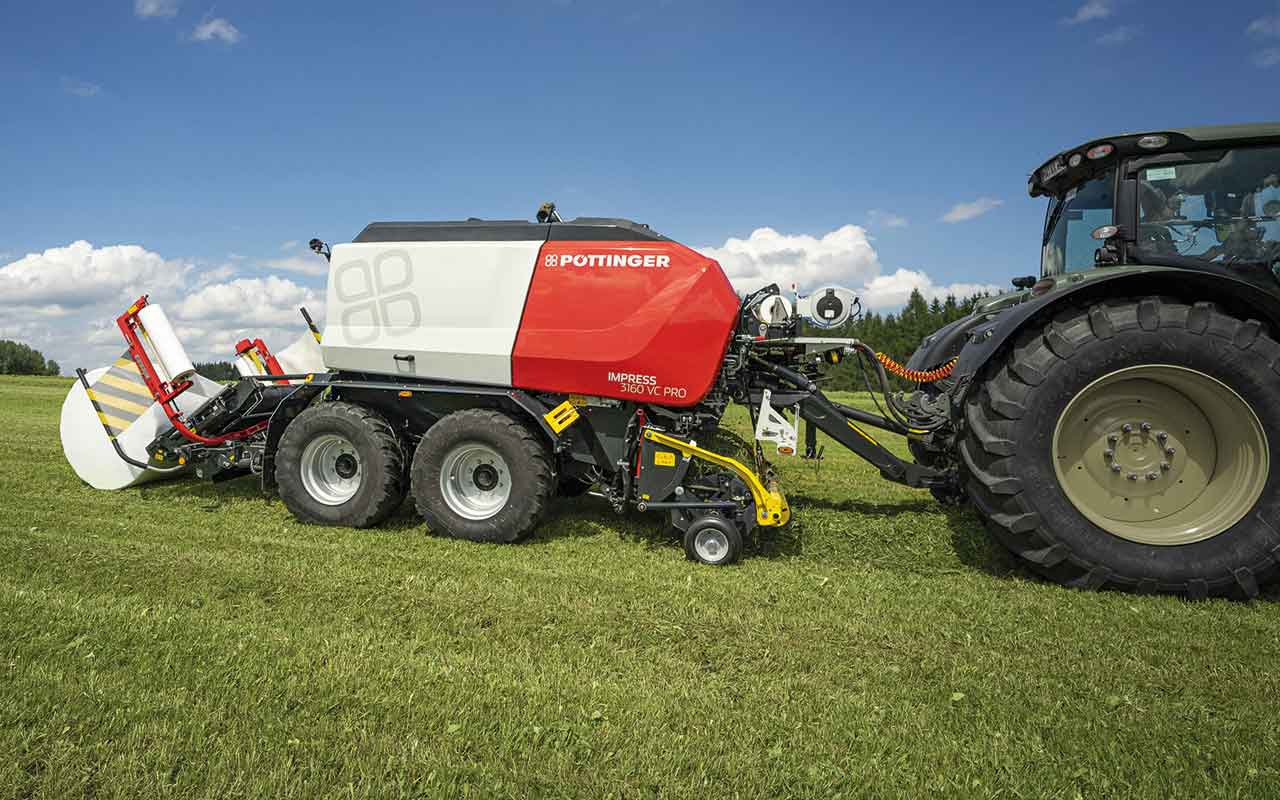
Pöttinger
The new generation of Pöttinger Isobus Impress 3000 Pro baler and wrapper combinations now features data transfers from the job computer.
Data can include bale weight, the number of bales and the moisture content of the bales, depending on the equipment options installed.
All the data collected using the Isobus interface can be saved for each job and sent to farm management software over the mobile phone network.
This lets you transfer data reliably, regardless of the tractor’s capabilities. Using Pottinger Connect Management, you can also display the live location of the machine.
Live location includes details of the weight and moisture content of the round bales, which can be used by contractors for invoicing purposes, or the farm to plan bale storage and use.
The Impress combination balers are available with a fixed or variable bale chamber, each with a floating pick-up and adjustable knife bank.
At the rear, the wrapping table is designed with the arms driven from below, keeping the centre of gravity close to the floor and ensuring there is no upper limit to stop larger bales moving through the machine.
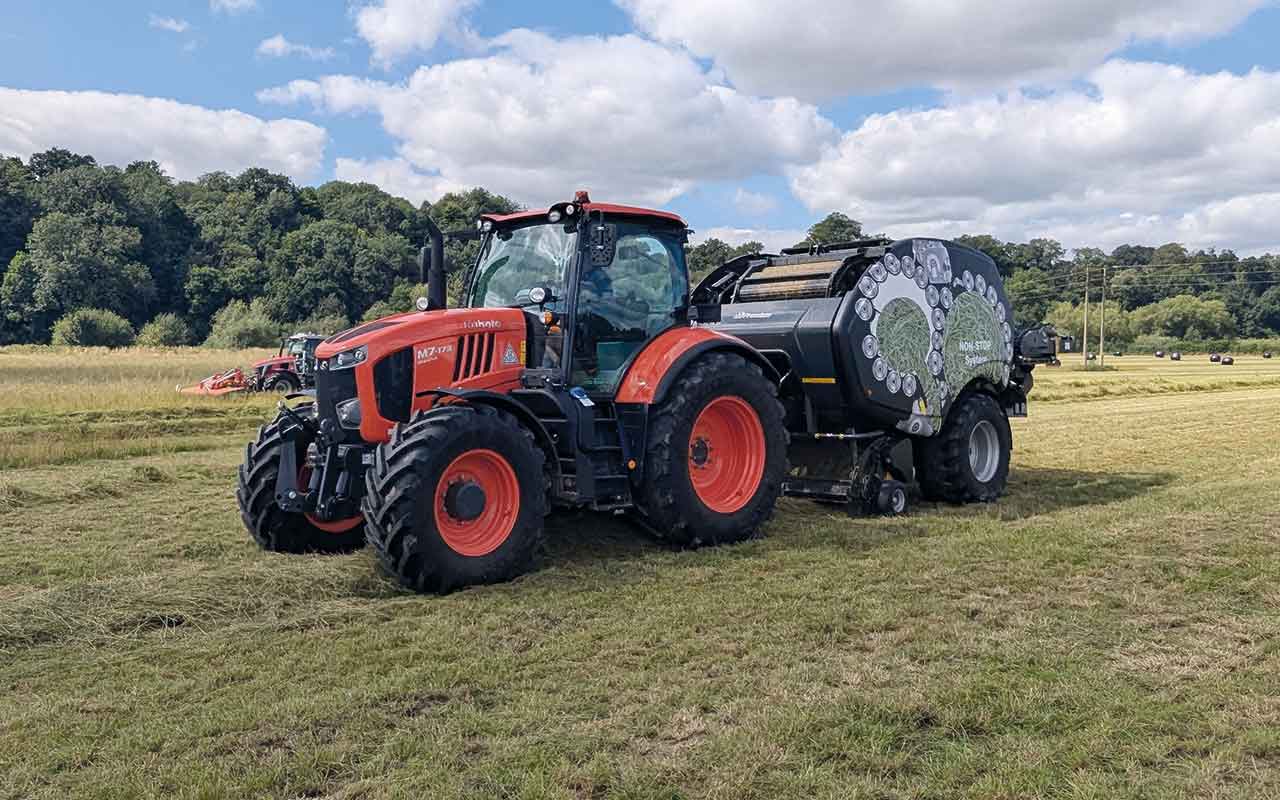
Vicon
The FastBale non-stop baler has been given new Premium branding and black livery. The company claims operators can save up to 20sec/bale, with spot rates hitting 90 bales/hour.
In addition to the standard bale chamber and rear-mounted wrapper unit, the FastBale has a pre-chamber that is two-thirds the size of the main chamber.
Key to the design is the gradual downward slope, starting at the pre-chamber and continuing through the larger chamber and onto the wrapping table. This means a bale in progress is always moving in a natural direction.
When operation starts, grass is fed directly into the main chamber. The 2.2m pick-up is equipped with five tine bars and a cam-track mounted at each end, to halve loadings and provide greater durability.
When chopping is required, the SuperCut system can be activated in groups depending on the required chop length.
When the first bale is complete in the main chamber, the netting system is activated. This can be specified for film-on-film wrapping.
The operator does not need to stop the baler when the netting starts, as the pre-chamber will open and start filling.
It has been designed so that, as the main chamber unloads the bale onto the wrapping table, the pre-chamber should be nearly full and ready to unload.